Understanding Business Operations Process Flow
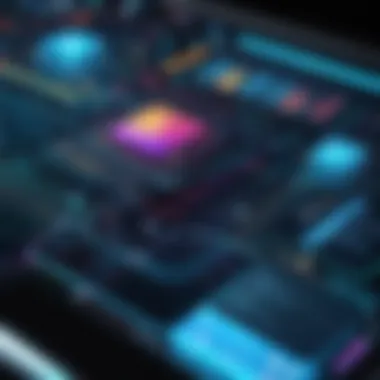
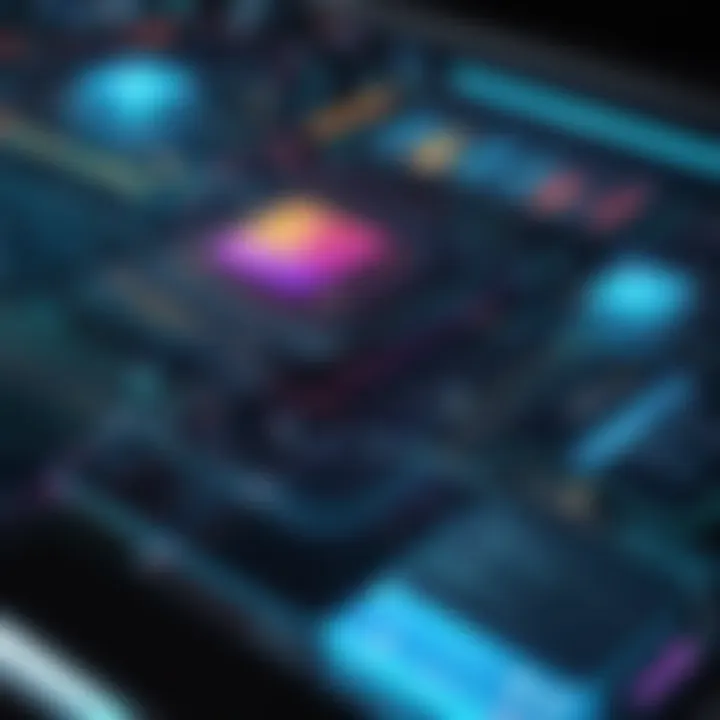
Intro
In today's competitive landscape, the way business operations flow can make or break an organization. Recognizing the need for better efficiency and effectiveness, companies are diving into the intricacies of their process flows. Understanding these flows is not just a administrative task; it's an art and science that combines strategy, technology, and human behavior.
Software Category Overview
Purpose and Importance
At its core, business operations process flow involves examining and refining the journey from inception to completion of a task within an organization. Whether a company is large or small, having a clear understanding of this flow helps to streamline operations, leading to better resource allocation, enhanced productivity, and improved outcomes. It serves as a roadmap, guiding employees through their daily activities efficiently. The right software tools here can facilitate that visualization, making it easier to spot bottlenecks and inefficiencies. Thus, their role cannot be overlooked.
Current Trends in the Software Category
With technology evolving at a rapid pace, businesses are increasingly leaning towards automation and data analytics in their process flows. Solutions like Asana, Trello, and Monday.com have surged in popularity as organizations seek not only to manage projects but also to deliver real-time insights into team performance.
Recent trends have shown that cloud-based software solutions are on an upward trajectory, allowing for greater flexibility and accessibility for teams that may be distributed across various locations. Companies are also starting to harness Artificial Intelligence capabilities. For instance, AI can sift through mountains of data to provide actionable insights, helping organizations avoid potential pitfalls in their operations. Reviewing these innovations provides essential context to understanding the comprehensive landscape of business operations.
"A successful process flow is one that not only meets the immediate needs but also adapts to future requirements and challenges."
Data-Driven Analysis
Metrics and Criteria for Evaluation
When evaluating business operations process flows, certain key metrics come into play. Time efficiency, resource allocation, and cost-effectiveness are fundamental elements every organization should scrutinize. Tracking these metrics provides concrete data for decision-making. Identifying key performance indicators (KPIs) is crucial:
- Cycle Time
- Cost Per Process
- Error Rate
- Customer Satisfaction
These metrics enable organizations to draw comparisons between current performance and established benchmarks, offering a clear picture of where improvements are necessary.
Comparative Data on Leading Software Solutions
A closer look at various software solutions available today can emphasize how they impact business operations process flows. SAP Business One, known for its comprehensive functionalities, offers robust analytical tools that cater primarily to medium-sized businesses. On the other hand, Zoho, appealing to a broader audience, boasts an array of integrated applications aimed at small enterprises.
As companies weigh their options, the decision often boils down to identifying what they truly need: a solution focusing on scalability or one prioritizing niche functionalities.
It's an intricate puzzle, but understanding the strengths and limitations of each option can lead to a more informed choice, ultimately impacting the efficiency of their processes.
Understanding Business Operations
When diving into the world of business operations, it's crucial to grasp what makes operations tick. Think of business operations as the lifeblood of an organization. They include everything from how tasks are completed to how resources are allocated. Understanding these nitty-gritty details not only informs key decision-making but also maximizes efficiency and drives organizational success.
- Importance of Understanding Business Operations: This understanding is essential for identifying inefficiencies, managing resources wisely, and optimizing the overall flow of business processes. It enables organizations to function like a well-oiled machine, where every part knows its role and contributes to the whole.
- Considerations: Organizations must take time to study the intricacies of their operations. This involves analyzing existing processes, pinpointing areas for improvement, and ensuring all team members understand their responsibilities, which can be challenging but is ultimately worthwhile.
Definition and Importance
Business operations refer to the ongoing activities a business undertakes to produce value and maintain its functions. This encompasses a wide array of tasks, including production, accounting, sales, and customer service. Each of these functions must work harmoniously for the organization to thrive.
Key points about Business Operations:
- Ensures efficient use of resources
- Enhances customer satisfaction
- Facilitates compliance and risk management
Understanding these components is not merely an academic exercise; it’s essential for designing strategies that enhance productivity. In this fast-paced environment, having a solid grasp on operations can distinguish successful companies from those that struggle.
Core Components
The core components of business operations are critical to fostering a productive work environment. At a high level, these can be split into several distinct yet interconnected areas:
- Process Management: This involves designing, monitoring, and refining processes to make them as effective as possible. Any hiccup in this area can negatively influence overall performance.
- Resource Management: This is about the strategic allocation and utilization of resources including human capital, technology, and finances to meet business objectives.
- Customer Management: Companies must understand their customers, as happy customers translate into repeat business. Gathering feedback and acting on it should be a persistent endeavor.
- Performance Management: It is crucial to measure and analyze the outcomes of various processes against set benchmarks. This can identify strengths and highlight weaknesses within the organization.
Understanding these core components helps businesses craft tailored strategies and foster an environment ripe for innovation and development. The synergy among these components form the foundation of robust business operations.
What is Process Flow?
Understanding process flow is crucial for anyone involved in the engine of business operations. It revolves around the smooth movement through different stages in a system, ensuring tasks progress efficiently. Whether you're in a start-up or a multinational corporation, the way you lay out your processes can spell the difference between chaos and success. A defined process flow can pinpoint bottlenecks, enhance productivity, and boost overall performance. Companies depend on it to streamline their activities and maximize output while minimizing resource wastage.
Basic Concepts
At its core, process flow refers to the sequence of activities or tasks that take place to achieve a particular goal. Think of it like a road map, guiding the journey from point A to point B. It helps in understanding how different functions interplay within an organization, guiding teams and individuals to perform their jobs effectively. Here are some key elements:
- Inputs and Outputs: Every process flow has specific inputs that trigger activities, leading to intended outputs. For instance, in a manufacturing setup, raw materials serve as inputs, and finished products are the desired outputs.
- Process Steps: These are the actions taken to transform inputs into outputs. Identifying each step is vital for refining operations.
- Flow Direction: This indicates how tasks progress – whether linearly, or in a more complex manner with loops and feedback.
Each of these components interlocks to create a coherent path that drives the organization forward. The clarity in these concepts ensures that everyone understands their roles, which is paramount in driving efficiencies.
Types of Process Flows
There are various types of process flows, each serving its own purpose. Choosing the right type can greatly influence the success of your project or organization:
- Linear Process Flow: This is the simplest form, where tasks are arranged in a sequential manner. Every step leads to the next, making it easy to follow. Think of it as a straight highway—ideal for processes needing minimal deviations.
- Parallel Process Flow: Here, multiple tasks occur simultaneously. This method can speed up operations significantly, as various teams tackle their parts of the project concurrently. It’s like different lanes on a busy road that operate independently.
- Cyclic Process Flow: In some cases, processes may need to revisit previous steps based on data feedback or outcomes. Such flows allow for adjustments and continuous improvement, not unlike a circular race track.
- Flexible Process Flow: This dynamic type accommodates changes in tasks or paths, allowing for adaptability in situations where the unpredictability of external factors is high.
Each type has its own nuances and lends itself to particular use cases. Understanding which to apply can lead to significant advantages when it comes to operational efficiency and flexibility.
"The flow of processes isn't just about moving forward; it's about moving smartly to enhance performance and avoid pitfalls."
In light of these concepts and types, it's evident that grasping process flow is indispensable for modern business operations. With the right processes in place, organizations can harness their resources more effectively and focus on achieving strategic goals.
Mapping Business Processes
Mapping business processes is a crucial step in streamlining the various functions of an organization. By visualizing workflows, it allows companies to see how tasks are interconnected and where inefficiencies might arise. Whether you are a seasoned business professional or an IT specialist, understanding how to map these processes effectively can have a significant impact on operational success.
One of the key elements in mapping business processes is clarity. Without a clear picture of how tasks flow from one to another, it’s easy for miscommunication and delays to occur. Moreover, mapping helps identify redundancies in processes, which can waste valuable time and resources. This creates an immediate benefit for organizations seeking to optimize their operations.
Benefits of mapping business processes include:
- Increased Efficiency: When every step is traced, it becomes easier to spot bottlenecks and eliminate unnecessary tasks, leading to faster turnaround times.
- Enhanced Collaboration: Different departments can understand how their work affects others. This attempts to foster better teamwork and communication.
- Improved Training: New employees can be onboarded faster with visual aids that summarize processes, resulting in reduced learning curves.
However, there are considerations to keep in mind. Not all workers may be comfortable with the mapping software, so training might be necessary. Moreover, while mapping can reveal inefficiencies, it can also overwhelm teams if the information is too complex. Thus, finding a balance between detail and usability is essential.
"Mapping processes is like navigating a vast sea; without a map, you risk losing your way."

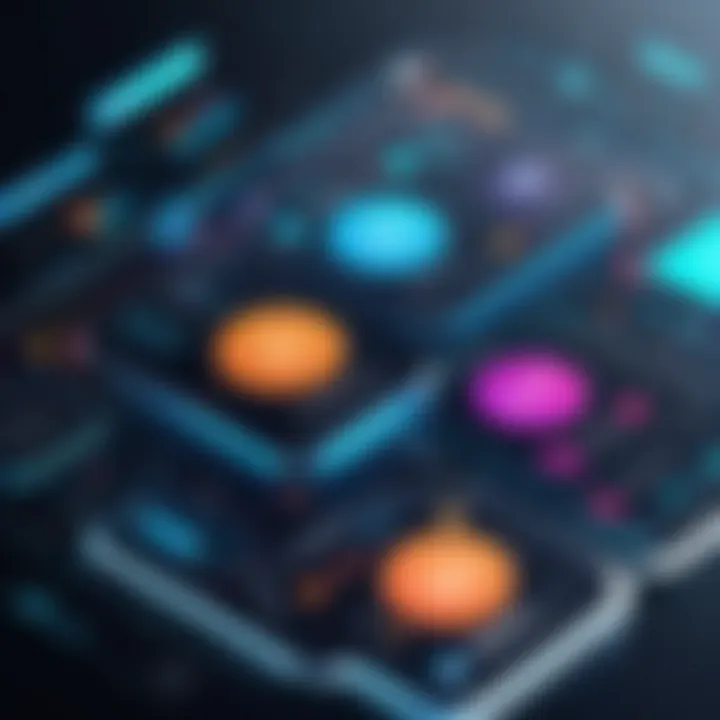
The Role of Flowcharts
Flowcharts play a significant role in the process mapping journey. These visual representations break down processes into understandable segments, allowing stakeholders to get a quick overview of workflows. Unlike traditional text-based documentation, flowcharts use symbols and arrows, which can make complex information easier to digest.
Using flowcharts enables businesses to:
- Visualize Complex Processes: Steps become easier to follow when laid out in a flowchart format.
- Identify Gaps: Clear representations can help pinpoint where things could go awry, facilitating timely corrections.
To create effective flowcharts, a few simple strategies can be applied:
- Start Simple: Begin with the main steps, then gradually add more detail where applicable.
- Use Standard Symbols: This helps maintain consistency and makes charts easier for everyone to understand.
- Collaborate: Involve relevant team members in developing the flowchart to gain insights that may otherwise be overlooked.
Tools and Techniques
Numerous tools and techniques are available for mapping processes, each offering unique features. Here are a few notable ones:
- Lucidchart: Great for creating flowcharts with collaborative features that allow multiple users to edit simultaneously.
- Microsoft Visio: A robust diagramming tool, particularly effective for large organizations with complex processes.
- Bizagi: This free option is perfect for those starting out, offering templates for various business processes.
When employing these tools, it's essential to keep the following techniques in mind:
- Involve Stakeholders: Getting input from everyone affected by the process can yield richer insights.
- Iterate: Process maps should not be static. Regularly revisiting and updating them ensures they remain relevant.
In summary, mapping business processes is not just about creating diagrams; it's about paving the way for efficiency and clarity in an organization's daily operations.
Analyzing Process Flow
In the bustling world of business operations, analyzing process flow holds a pivotal role. It signifies the point at which organizations step back, take a long hard look at their inner mechanics, and identify where the proverbial wheels might be squeaking. By embarking on this analytical journey, businesses can unveil inefficiencies, streamline workflows, and ultimately enhance productivity.
Identifying Bottlenecks
One of the principal components of analyzing process flow is pinpointing bottlenecks. These are constrictions in the work process that can hinder progress, leading to a domino effect of delays downstream. Recognizing these choke points is like shining a flashlight in a dark room; it brings hidden obstacles into view.
Bottlenecks may arise from various sources: limited resources, outdated technology, or even procedural redundancies. For instance, picture an assembly line where a single machine is lagging behind—each hiccup here delays the entire production output. Thus, businesses can benefit significantly from mapping out their processes with a keen eye on where things slow down.
A few techniques for identifying these bottlenecks include:
- Flowcharts: Simple visual representations can help highlight where delays occur.
- Process Simulation: Running models of the processes allows businesses to see where resources are overloaded.
- Feedback Loops: Gathering insights from employees involved in the process can help elucidate practical issues that might not be immediately visible.
To quote a wise saying, "A chain is only as strong as its weakest link," underscoring the need to address these bottlenecks for a robust process flow.
Data Collection Methods
The importance of data in analyzing process flow cannot be overstated. It acts like the compass guiding organizations through the maze of their operations. However, the right methods for data collection must be in place to gather meaningful insights.
First off, it’s crucial to distinguish between qualitative and quantitative data. Qualitative data might come in the form of employee interviews or surveys, while quantitative data involves numerical metrics, such as output rates or error counts. Utilizing both types ensures a well-rounded view of operations.
Several data collection methods suited for this purpose include:
- Surveys and Questionnaires: Gauge employee experiences and collect suggestions on potential improvements.
- Time Studies: Measure the time taken for each subprocess to identify areas that consume excessive time.
- Software Analytics: Many businesses deploy tools that track operational metrics, providing real-time insights into performance.
Implementing a combination of these methods creates a dataset that reveals trends and patterns, offering a detailed landscape of performance. Therefore, a comprehensive approach to data collection becomes instrumental in sculpting a more efficient process flow.
Optimizing Process Flow
Optimizing process flow is a crucial aspect of business operations, impacting every facet from efficiency to cost management. In a fast-paced market, businesses must adapt and improve their workflows to keep pace with competitors. This not only boosts productivity but also enhances customer satisfaction and drives profitability. Thus, understanding how to effectively optimize process flow cannot be overstated.
At its core, optimizing process flow involves evaluating existing workflows and identifying opportunities for enhancement. This may include streamlining procedures, reducing waste, and ultimately ensuring that each step of the process adds value. The benefits are manifold: they can lead to shorter delivery times, reduced operational costs, and an overall improved workplace atmosphere. Most importantly, it creates a culture of continuous enhancement—a mindset that fosters innovation.
Principles of Lean Management
Lean management is a foundational approach to process optimization, focusing on value creation while minimizing waste. This principle hails from the manufacturing sector, particularly the Toyota Production System. However, its applicability spans across various industries today.
Key principles of lean management include:
- Value Stream Mapping: This involves outlining all actions in a process and identifying which ones add value for the customer and which are deemed waste. It helps visualize the entire workflow, making it easier to pinpoint inefficiencies.
- Continuous Improvement (Kaizen): The philosophy behind Kaizen is that small, incremental changes lead to significant improvements over time. Every employee, from the CEO to factory floor workers, is encouraged to propose changes for the betterment of the process.
- Just-In-Time (JIT): JIT emphasizes the importance of producing the right amount of product at the right time without excess inventory. This creates a responsive system that can adapt quickly to changes in demand.
Each of these principles plays a critical role in eliminating waste and enhancing efficiency. When organizations incorporate lean management techniques into their operations, they often find that decision-making becomes quicker, and the entire business is more agile.
Continuous Improvement Models
Continuous improvement models represent strategies that organizations employ to constantly push for better performance. The philosophy of continuous improvement operates under the belief that no process is ever 'perfect' and that there’s always room for enhancement.
A few popular models include:
- PDCA (Plan-Do-Check-Act): This model promotes iterative cycling through four stages. Initially, a plan is developed to improve a process. Then, the plan is implemented. After that, results are checked against the desired outcome, and based on findings, actions are taken to refine the plan for future iterations.
- Six Sigma: This methodology seeks to improve quality by identifying and removing causes of defects and minimizing variability in manufacturing and business processes. It uses a data-driven approach and statistical tools to guide decision-making.
- The DMAIC Framework (Define, Measure, Analyze, Improve, Control): This framework is a subset of Six Sigma used predominantly for improving existing process flows. It guides teams through structured stages to pinpoint problem areas and implement solutions effectively.
Implementing these models can generate significant benefits, such as reducing variability, increasing quality, and ensuring a consistent experience for customers.
"Challenges in optimizing process flow often arise, not from a lack of resources, but from narrowed perspectives. Broadening the scope is essential to uncover potential improvements."
In sum, optimizing process flow is not just an operational enhancement but a strategic imperative. Leveraging principles of lean management alongside dynamic continuous improvement models ensures that organizations remain relevant in a constantly changing market landscape.
Implementing Process Reengineering
Implementing process reengineering stands as a crucial tactic within the broader context of business operations. Its importance lies not only in refining existing workflows but also in fundamentally reshaping how organizations approach their objectives. This transformation can pave the way for increased efficiency, reduced operational costs, and enhanced customer satisfaction.
When organizations decide to embark on this journey, they are often met with a host of specific elements that need careful consideration:
- Assessment of Current Processes: Understanding what currently exists is a vital starting point. One must examine the workflow deeply, identify redundancies, and pinpoint barriers that hamper productivity. This analysis will lay the groundwork for what needs change.
- Defining Clear Objectives: A successful reengineering effort hinges on well-articulated goals. Whether it's improving service speed, boosting quality, or streamlining communication, these objectives need to be straightforward and communicated consistently across the organization.
- Stakeholder Engagement: Engaging with those who will be affected by the changes is critical. By involving employees in the planning stages, you gain valuable insights while also fostering a sense of ownership, greatly enhancing the chances of a smooth transition.
Strategic Considerations
In the realm of process reengineering, strategy shapes every choice made. Implementing substantial changes requires aligning these shifts with the company’s overarching goals.
- Market Adaptability: Companies must remain responsive to the evolving market landscape. This may include shifting customer preferences or emerging technological tools that redefine standards. Successful reengineering will not only address present challenges but also position the business favorably for future disruptions.
- Resource Allocation: Resources—be it human capital, technology, or finances—must be evaluated with an eye towards reallocation. Investing in technology that accelerates processes or training programs for staff can yield significant dividends down the line.
- Performance Metrics: Establishing measurable benchmarks is essential for monitoring the effectiveness of implemented strategies. Metrics offer insight into what’s working and what may require further adjustment to ensure continued alignment with business objectives.
Change Management Essentials
Equally important as the reengineering itself is how changes are managed within the organization. Change management is the backbone that supports individuals through transitions and helps ensure that the reengineering efforts yield the desired outcomes.
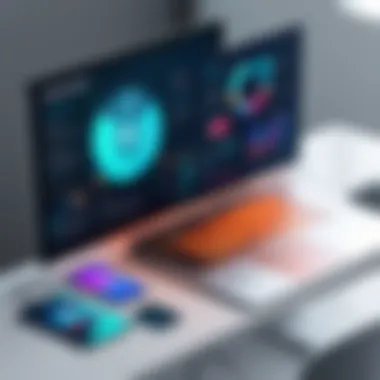
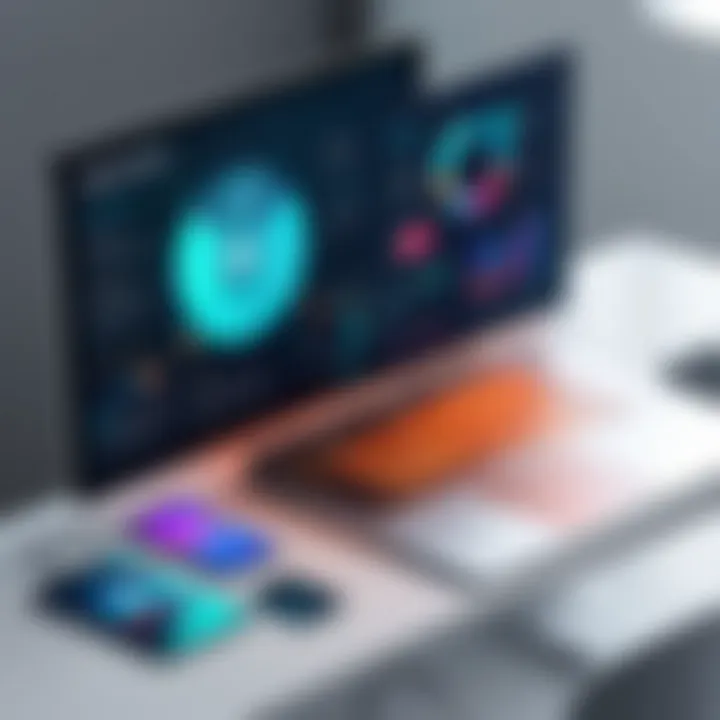
- Communication: Clear, transparent communication is fundamental in change management. Employees should be kept in the loop about what changes are happening, why they’re necessary, and how they will benefit both the organization and the personnel.
- Training and Support: When new processes are put in place, employees must be equipped to adapt. This can involve comprehensive training sessions that not only cover new procedures but also address any technological tools introduced.
- Feedback Mechanism: Establishing channels for feedback allows employees to voice concerns or offer suggestions. This participatory approach not only enhances morale but can also reveal potential issues before they escalate into bigger problems.
"Reengineering is not just about changing processes but creating a culture that embraces change."
Ultimately, the implementation of process reengineering is an intricate dance between strategy and tactile execution. By focusing on these essentials—strategic considerations, stakeholder involvement, and robust change management—organizations can navigate the complex waters of transformation with greater ease, ensuring they emerge stronger and more agile in an ever-competitive environment.
Technology's Role in Process Flow
In today's fast-paced business landscape, the role of technology in refining process flow cannot be underestimated. Organizations, whether they're running on a small scale or operating at enterprise levels, find themselves leaning on technology to boost efficiency, reduce errors, and drive innovation. The integration of technology into business processes is akin to adding a turbocharger to a car; it provides the necessary thrust to accelerate growth and operational capabilities.
Utilizing advanced technologies transforms mundane tasks into streamlined operations. Companies can achieve greater control, consistency, and visibility across their processes. The adoption of specific elements such as automation tools and tailored software solutions is paramount for organizations that want to position themselves ahead of the curve.
Automation Tools
Automation tools have revolutionized how businesses manage their operations. At the core of this shift is the ability to reduce the manual workload for employees while minimizing human error. Implementing automation within business processes can mean the difference between a company that scrambles to meet demands and one that flows smoothly through its operational challenges. Here are some noteworthy aspects of automation tools that deserve attention:
- Enhanced Efficiency: Automated systems take over repetitive tasks like data entry, report generation, and inventory management. This allows staff to concentrate on more strategic tasks, which can lead to better decision-making and innovation.
- Cost Reduction: By minimizing the need for manual oversight, businesses can cut down on labor costs and errors that can lead to waste or customer dissatisfaction.
- Improved Accuracy: Automated solutions often operate with a high degree of precision, thus reducing discrepancies and elevating the quality of data analytics.
Ultimately, adopting automation is not just about technology—it's about fostering a culture of efficiency and accountability. It becomes feasible to track workflows and measure improvements over time, allowing companies to pivot when necessary.
Software Solutions
Software solutions offer a broad range of tools tailored to enhance various business processes. Unlike one-size-fits-all programs, modern software solutions provide nuanced capabilities catered to specific needs. Here’s how software can impact business operations:
- Centralization of Information: With cloud-based systems, data from disparate departments can be unified. This enables real-time collaboration, ensuring all stakeholders have access to the information they need when they need it.
- Scalability: As a company grows, software solutions can adapt and expand. Whether it’s incorporating additional users, integrating new features, or connecting with other business systems, modern software is designed to grow with the business.
- Data-driven Insights: Advanced analytics embedded within software solutions empower businesses to derive meaningful insights from their data. With tools like dashboards, companies can visualize key performance indicators effectively, steering strategic decisions.
"Technology, when leveraged correctly, can be a game changer, turning complex processes into streamlined and efficient workflows."
Furthermore, the synergy between automation tools and software solutions can create a robust ecosystem where data flows seamlessly, and processes adapt in real-time to changing market demands. For tech-savvy individuals and business professionals, the imperative is clear: embracing technology isn't just beneficial; it's essential for current and future success.
Case Studies in Process Flow
In the realm of business operations, analyzing real-world case studies in process flow serves as a powerful lens through which organizations can draw valuable insights. Such studies not only illustrate the practical application of theoretical concepts but also highlight the dynamic nature of process flow management. By examining the successes and failures of various organizations, businesses can glean lessons that inform their own operational strategies. Positioned strategically, these case studies can function as both guiding lights and warning tales that aid in navigating complex environments.
Success Stories
Success stories in business process flow don't just serve as a rah-rah for management, they offer concrete examples of what good looks like. Take a look at the manufacturing giant Toyota, renowned for its production system—commonly referred to as lean manufacturing. The company integrated principles of waste reduction, time savings, and efficiency to create a model that others aspire to replicate.
For instance, by utilizing Just-In-Time (JIT) inventory systems, Toyota managed to drastically cut down its stock levels. In this method, components arrive at the assembly line just when they are needed, minimizing excess inventory costs and reducing waste. The impressive results were not merely about improved sales; Toyota reported significant declines in operational costs and improved customer satisfaction ratings. Such examples showcase that a meticulous approach to process flow can yield remarkable results.
Additionally, another fascinating case is that of Zara, the fast-fashion retailer. Zara operates on a model that emphasizes rapid production and distribution, allowing them to introduce new styles at a dizzying pace. By implementing a responsive supply chain and efficient production processes, they can get a product from concept to store in a matter of weeks. This agility is advantageous not just in capturing trends but also in managing inventory and resources effectively, thus leading to higher profitability. In essence, success stories like these prove that optimizing business operations process flow can lead to sustainable competitive advantage in a crowded market.
Lessons Learned from Failures
While triumphs in business are a great source of learning, failures provide an equally essential viewpoint. Consider the classic example of Kodak, which offers a poignant lesson about process flow management in the digital age. Despite its dominance in the photography industry, Kodak failed to adapt its processes to the growing digital photography trend, sticking to its film model far too long. This resistance to change resulted in the company filing for bankruptcy in 2012, showcasing how stagnant process flow can cripple even the most established businesses.
Another notable failure is that of the Target expansion into Canada. The retailer aimed to streamline operations and open new stores in a short timeframe. However, they faced severe stock issues resulting from a poorly calibrated supply chain. Their process flow was misaligned with logistics needs, leading to empty shelves and glaring customer dissatisfaction. Ultimately, this misstep cost Target billions and forced them to withdraw from the Canadian market altogether.
These cautionary tales reveal how weaker process flows can lead to dire consequences. The crux here is to remember that maintaining agility and foresight within operational processes is central to avoiding pitfalls. Learning from such experiences can inform efforts to revamp and reinvigorate process management strategies.
In summary, whether through success stories or lessons from failures, the study of case studies in process flow provides businesses with the real-world insights needed to refine their operations. By learning from the past, organizations can better navigate the complex landscape of business process management today.
Measuring Process Efficiency
Understanding process efficiency is critical for any organization that aspires to thrive in today’s competitive marketplace. The significance of measuring process efficiency lies in its potential to unveil how well an organization utilizes its resources—be it time, money, or manpower. When businesses commit to this measurement, they not only identify areas that need improvement but also set the stage for enhanced productivity and cost-effectiveness. In essence, measuring process efficiency isn't just about numbers; it reflects the pulse of the operational heartbeat.
KPI Development
Key Performance Indicators, or KPIs, are essential for quantifying the effectiveness of any process flow. These indicators act like the compass guiding an organization toward its strategic objectives. Developing robust KPIs involves a multi-faceted approach:
- Clear Objectives: You must be crystal clear on what you want to achieve. If the goal is to reduce operational costs, then the KPIs should mirror that aim. For example, a KPI might track the cost per unit produced.
- Data-Driven Metrics: Relying on subjective assessments is like navigating without a map. KPIs should be grounded in data that can be measured consistently over time. Metrics like cycle time, throughput, and defect rates help provide a transparent view of process performance.
- Align with Organizational Goals: Ensure that the KPIs not only focus on process efficiency but also dovetail with the broader objectives of the organization. This alignment ensures that every department is pulling in the same direction. For example, if enhancing customer satisfaction is an overarching goal, metrics related to order delivery times should be included in the KPI framework.
- Regular Review and Adjustment: Just as stars shift with season, your KPIs need to be revisited regularly. This allows organizations to adapt to changing business landscapes, ensuring that the indicators remain relevant and aligned with current objectives.
Analyzing Performance Metrics
Once KPIs are set into motion, the next step is to analyze performance metrics effectively. This thorough examination reveals how well processes contribute to overall efficiency and effectiveness:
- Visual Dashboards: Utilizing visual tools and dashboards can simplify the interpretation of complex data. A visual dashboard presents metrics in an easily digestible format, enabling quick decision-making. Consider tools like Tableau or Power BI that can visualize large sets of data and highlight inefficiencies.
- Trend Analysis: Observing trends over time provides insights beyond snapshots offered by singular data points. It helps in understanding seasonality and the long-term trajectory of performance metrics, allowing for proactive adjustments. For instance, identifying a consistent increase in defect rates could prompt investigations before the problem escalates.
- Benchmarking: Comparing metrics against industry standards acts as a reality check. It allows businesses to measure their performance relative to competitors, shedding light on potential areas for improvement. Identifying gaps often leads to innovative solutions that can leapfrog an enterprise ahead.
"If you can’t measure it, you can’t improve it."
– Peter Drucker
To Conclude
Measuring process efficiency, especially through thoughtful KPI development and in-depth analysis of performance metrics, forms the cornerstone of any organization’s operational strategy. Each metric provides insight into different facets of the process flow, and the clearer the understanding of these metrics, the more agile and responsive the organization can be.
By focusing on these aspects, businesses can not only streamline operations but also enhance their competitive edge—positioning themselves for sustainable growth in a rapidly evolving landscape.
Challenges in Process Flow Management
Understanding the challenges that arise during process flow management is crucial for any organization seeking efficiency and effectiveness. Managing processes is not merely about establishing clear paths; it involves navigating a landscape filled with potential obstacles. These challenges can impede progress, waste resources, and ultimately compromise an organization's goals. By acknowledging and addressing these challenges, businesses can foster a more resilient operational framework that leverages optimal process flows to drive success.
Resistance to Change
Resistance to change is a significant hurdle many organizations face. Even when there's a clear need for improvement in process flow or the introduction of new tools, staff may cling to established routines. This resistance can stem from a fear of the unknown, a belief that current systems work well enough, or concerns about job security. Understanding the psychology behind this resistance is key. Employees want to feel secure in their roles and comfortable with their tasks. When changes are imposed without clear communication or training, it can lead to frustration and increased operational errors.
To combat resistance, it is essential for management to foster a culture of openness. This includes:
- Communication: Clearly articulating the reasons for change, the benefits it brings, and how it aligns with the organization’s goals.
- Involvement: Engaging staff in the change process, allowing them to voice concerns and contribute ideas.
- Support: Providing necessary training to ensure that all employees are prepared to embrace new systems or procedures.
By addressing the root causes of resistance, organizations can pave the way for smoother transitions and more successful implementations of process flow optimizations.
Resource Allocation Issues
Resource allocation can often become a thorny issue, especially in complex organizations where multiple projects compete for attention and funding. Inefficiencies can arise when resources—whether they be financial, human, or technological—are not distributed wisely. Misallocation can lead to delays, bottlenecks, and dissatisfaction not just among employees but also with clients who expect timely deliveries and high-quality outcomes.
Several considerations can help mitigate resource allocation issues:
- Prioritization: Evaluating projects and determining which have the highest potential return on investment can optimize resource distribution. Prioritizing effectively ensures that critical initiatives have what they need to succeed.
- Transparency: Maintaining clear visibility into how resources are being utilized allows for better tracking and adjustments. Stakeholders should be informed about resource use and be able to raise concerns when they feel certain allocations are mishandled.
- Agility: The ability to reallocate resources swiftly in response to changing demands or challenges is vital. An agile approach allows for real-time adjustments that can prevent major disruptions in workflow.
Effectively managing resource allocation helps ensure that process flows remain unimpeded, promoting a healthier work environment and enhancing overall productivity.
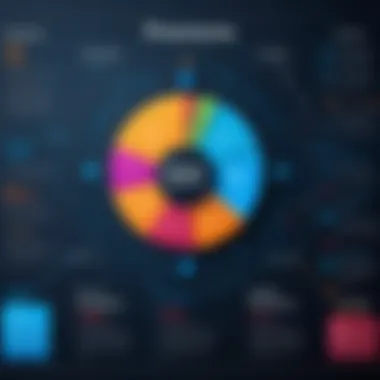
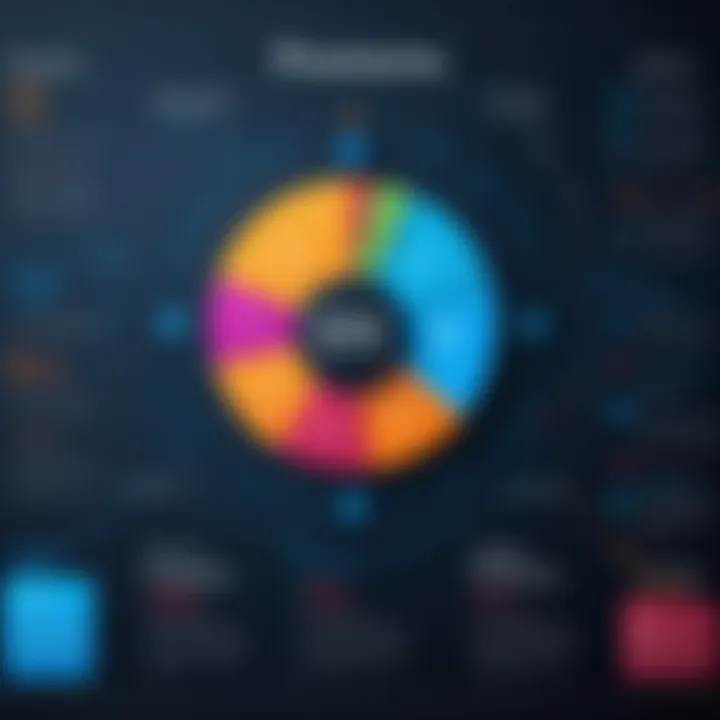
"Change is the law of life. And those who look only to the past or present are certain to miss the future." - John F. Kennedy
Navigating these challenges in process flow management is not a one-time fix but an ongoing effort. By consistently assessing and refining strategies to address resistance to change and resource allocation, organizations can create a more streamlined operational approach that leads to sustained improvement and growth.
Best Practices in Business Process Flow
Understanding and implementing best practices in business process flow is crucial for any company aiming to maximize efficiency and productivity. It’s not just about streamlining operations, but about creating a culture of continuous improvement that positively impacts the bottom line. Applying best practices helps to minimize errors, reduce waste, and enhance collaboration across teams.
Here are several critical elements and considerations for establishing effective practices in business process flow:
- Consistency: Establish a standard approach to how processes are documented and executed. This minimizes variation and confusion.
- Clarity: Ensure everyone involved understands their roles and the process itself. This can decrease bottlenecks that often plague operations.
- Feedback Loops: Create mechanisms for receiving ongoing feedback from all stakeholders involved in the process.
Documentation and Standardization
Thorough documentation is a linchpin in effective business process flow. When processes are clearly documented, it acts as a guiding light for employees. It allows for immediate reference, which is particularly valuable when onboarding new team members. Not only does this save time, but it also ensures everyone is on the same page.
Standardization goes hand in hand with documentation. By standardizing processes, businesses can ensure that operations are executed consistently every time. This reduces variability, leading to more predictable outcomes. To implement this effectively, consider the following steps:
- Develop Process Maps: These visuals create clarity, showing the step-by-step procedures involved.
- Use Templates: Create templates for essential documents that are often used. This shall help maintain uniformity.
"The devil is in the details; documenting processes helps you catch the small snags before they turn into big issues."
Engaging Stakeholders
Engaging stakeholders is often overlooked but is paramount to successful business operations. Active participation from all levels of the organization—management, staff, and often external partners—ensures that diverse perspectives are considered. Here are beneficial strategies to actively involve stakeholders:
- Regular Meetings: Create a routine to discuss processes, solicit input, and ensure alignment.
- Training Sessions: Offering training not only educates stakeholders but also empowers them to contribute more effectively to the process.
- Surveys and Feedback Forms: Use these tools to gather insights about the processes from those who engage with them daily.
These strategies lay the groundwork for a more collaborative environment, ultimately leading to enhanced productivity and satisfaction across the organization. Leveraging stakeholder engagement can create an atmosphere where everyone feels valued and heard, translating to a more committed workforce.
Future Trends in Process Flow Management
In the ever-evolving landscape of business operations, understanding future trends in process flow management is essential for organizations looking to maintain a competitive edge. These trends are not mere passing fancies; they represent profound shifts that influence how companies refine their operations, engage with stakeholders, and harness technology in their favor. The onus is on business professionals and IT specialists to stay ahead of the curve, as forecasting these trends can mean the difference between thriving and merely surviving in a crowded marketplace.
Several key elements shape this future, and their significance can’t be overstated:
- Dynamic Adaptability: Companies are increasingly required to be nimble. The ability to swiftly respond to market changes without losing efficiency is paramount.
- Data-Driven Decisions: The reliance on data analytics is growing. Insights drawn from consumer behavior and market trends are crucial for making informed choices about process improvements.
- Integration of AI and Automation: Automating routine tasks frees up human capital for more strategic initiatives. The merger of AI with operational processes cannot be overlooked.
"The future belongs to those who prepare for it today." - Malcolm X
Emerging Technologies
Emerging technologies are at the forefront of this transformation. The integration of technologies such as artificial intelligence, machine learning, and blockchain is reshaping how businesses approach process flow management.
- Artificial Intelligence: AI is changing the game. With capabilities like predictive analytics, organizations can foresee potential bottlenecks and address them proactively, minimizing disruptions to the workflow. Companies like Google and IBM are pioneering AI applications to streamline operations.
- Machine Learning: This technology enables systems to learn and improve from experience. Machine learning helps in refining process strategies by analyzing patterns and trends in operational data.
- Blockchain: While often associated with cryptocurrencies, blockchain has broader applications in process flow. Its decentralized nature enhances transparency and traceability, particularly valuable in supply chain management.
- Internet of Things (IoT): Connected devices can collect and transmit data in real-time, providing insights that were once elusive. Businesses leveraging IoT tools can monitor performance and make adjustments on the fly.
Shifts in Business Paradigms
As we venture into the future, shifts in business paradigms are giving rise to a new operational ethos. No longer can businesses afford to operate in silos or traditional hierarchies.
- Agile Methodologies: The adoption of agile practices is becoming widespread, enabling cross-functional teams to collaborate more efficiently. This approach allows faster responses to feedback and changes, enhancing the overall process flow.
- Customer-Centric Operations: Increasingly, the focus is on the customer experience. Organizations are aligning their processes more closely with customer needs and expectations, making adaptations based on direct feedback and engagement.
- Sustainable Practices: The urgency for sustainable operations is reshaping strategies. Businesses are now prioritizing processes that reduce waste and support environmental responsibility, becoming not just profit-driven but also purpose-driven.
- Collaborative Ecosystems: Companies are learning that working with partners, customers, and even competitors can yield better results. Sharing information and resources can enhance flexibility and innovation across the board, creating a win-win scenario.
Integrating Process Flow into Business Strategy
Integrating process flow into a business strategy is not just a nice-to-have; it’s essential for both small and large enterprises wanting to thrive in today’s fast-paced environment. When organizations align their operational processes with strategic goals, they pave the way for enhanced efficiency, clear direction, and measurable outcomes. Ignoring this critical integration can leave a business adrift, with processes that don’t support its objectives.
Importance of Integration
The integration of process flow into business strategy serves several purposes. Primarily, it ensures that every operational aspect is fine-tuned to contribute towards overarching goals, whether it be increasing customer satisfaction or reducing operational costs. Employees have clarity on how their roles impact the larger picture, which boosts engagement and productivity. When process flows are well connected to the strategy, businesses often see a marked improvement in both performance and culture.
- Benefits of Integration:
- Enhanced Cohesion: Ensures all departments work towards a unified aim.
- Improved Decision Making: Provides a clearer path for making informed choices.
- Greater Flexibility: Facilitates quicker adjustments as market conditions transition.
- Customer Focus: Align operations with customer needs and expectations.
Now let's delve deeper into the specifics of how to align goals with operations.
Aligning Goals with Operations
To align goals with operations, a business should start by clearly defining its strategic objectives. This should involve collaboration across various levels of the organization. An open dialogue will ensure that every team member understands not just the 'what' but also the 'why' behind the goals.
Once the objectives are set, operational processes must be scrutinized. It may turn out that there are activities that are unnecessary or misaligned. Streamlining operations not only cuts costs but can also increase agility. In connecting day-to-day operations with strategic intents, businesses also make their operations more transparent.
“A good strategy is about making choices; a great one is about making them operational.”
Key Steps for Aligning Goals with Operations:
- Define Strategic Objectives: Clearly state what the business aims to achieve.
- Map Current Processes: Create a visual representation of existing operations to identify areas of improvement.
- Identify Key Performance Indicators (KPIs): Use metrics that will help track the success of aligning processes with goals.
- Iterative Feedback: Regularly revisit goals and processes to ensure they remain in sync.
As operations come in line with strategic goals, it's vital to measure and evaluate the outcomes to see if the integration has been successful.
Evaluating Outcomes
Evaluating outcomes isn’t just about looking at results; it’s about understanding whether the integration of process flow has had the desired impact on the organization’s goals. This step involves analyzing performance metrics established earlier and determining if they reflect the strategic objectives effectively.
Key aspects of evaluating outcomes include:
- Data Analysis: Employ data analysis to dive deep into KPI performance. Look for trends that tell the narrative of success or failure.
- Stakeholder Feedback: Engage all relevant parties in discussions about what’s working and what isn’t. They often provide insights missed by higher-ups.
- Adjustment Planning: Use the evaluation phase to develop a roadmap for any necessary adjustments. The key to success is adaptability.
Ultimately, the ability to connect operational processes with strategic ambitions can define the health of an organization. Those that succeed in these integrations often find themselves on a trajectory toward lasting success.
Concluding Thoughts
In an era of constant evolution, the significance of refining business operations through well-structured process flow cannot be overstated. The comprehensive discussions throughout this article have illuminated how an organization’s success hinges not just on its goals but also on the efficiency of its operations. Having a robust understanding of business process flow empowers businesses to navigate complexities that arise in daily operations. It is crucial to recognize that process flow is not a one-size-fits-all solution; different organizations require tailored approaches that reflect their unique challenges and aspirations.
Summary of Key Points
- Understanding Importance: Effective process flow enhances productivity and reduces operational bottlenecks, ultimately paving the way for increased profitability.
- Practical Insights: Various tools and methods for analyzing, optimizing, and reengineering processes were explored, showcasing how proper oversight can bear fruit in both small and large enterprises.
- Emphasis on Collaboration: Engaging stakeholders and fostering a culture of communication are pivotal in harmonizing efforts across departments, ensuring that everyone is on the same page.
- Continuous Improvement: The necessity for ongoing evaluation and adaptation to change remains key to maintaining a competitive edge.
The Future of Process Flow in Business
The dynamics of business operations are poised for dramatic shifts with the rise of new technologies and methodologies. Emerging trends suggest that automation will play an increasingly paramount role, allowing organizations to streamline tasks that were once time-consuming. As Artificial Intelligence continues to advance, its integration into process flow management will become a game changer, driving efficiency like never before. Moreover, the shift towards digital transformation pushes businesses towards agile methodologies that prioritize adaptability.
"Adapting to the ever-changing landscape is essential; failure to innovate might result in falling behind one's competitors."
Furthermore, organizations must be cognizant of the evolving regulations and market expectations that shape operational methodologies. With the rise of sustainability concerns, future business models may prioritize eco-friendly practices integrated into process flows. Hence, maintaining an open mind toward emerging practices and tools can be the difference between thriving and merely surviving in this relentless landscape.
In summary, the exploration of business operations process flow reveals its multifaceted nature and undeniable importance. While challenges will undoubtedly arise, the potential for enhanced efficiency and success remains within reach for those willing to adapt and innovate.