Comprehensive Insights into Stock Planning Strategies
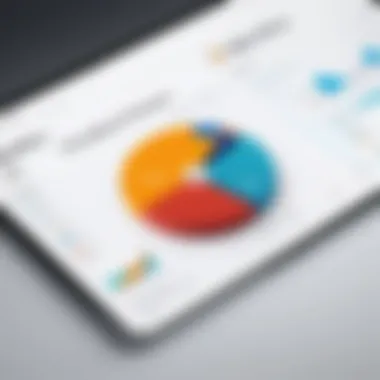
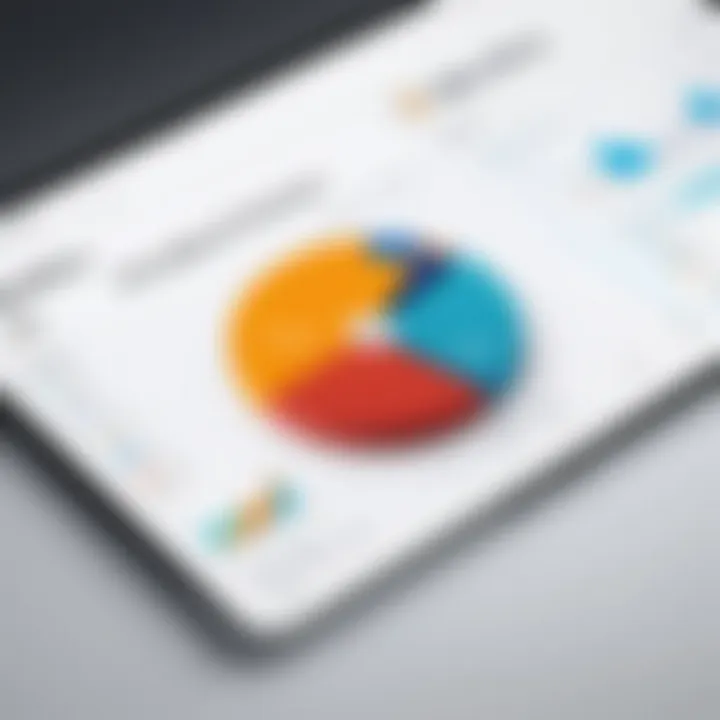
Intro
Effective stock planning is crucial in optimizing inventory levels, directly impacting a business's profitability and efficiency. As companies navigate complex market dynamics, understanding the methodologies and tools at their disposal to manage stock becomes increasingly important. Proper stock management can reduce costs, increase operational efficiency, and enhance customer satisfaction.
Software Category Overview
Purpose and Importance
In the realm of stock planning, software plays an integral role in ensuring supply chains operate smoothly. These tools provide businesses with functionalities to manage inventory levels, forecast demand, and streamline procurement processes. By automating these tasks, businesses can reduce human error, improve accuracy, and allocate resources more effectively.
Additionally, it allows organizations to harness data analytics, driving strategic decisions based on accurate insights. Effective stock planning software supports real-time data tracking, ensuring visibility into stock levels and forecasted demand trends. This enables decision-makers to react promptly to market changes and consumer behavior.
Current Trends in the Software Category
The stock planning software landscape is evolving. Recent trends highlight the integration of artificial intelligence and machine learning, making forecasting models more sophisticated. These advancements allow predictive analytics to offer personalized insights into customer preferences and purchasing patterns.
Moreover, cloud-based solutions are gaining traction due to increased accessibility and enhanced collaboration among stakeholders. Furthermore, the push towards sustainability is prompting software developers to incorporate features that enable more eco-efficient stock management practices.
Data-Driven Analysis
Metrics and Criteria for Evaluation
Evaluating different stock planning software requires a set of clear metrics and criteria. Key performance indicators (KPIs) that should be considered include:
- Inventory Turnover Ratio: Measures how often inventory is sold and replaced over a period.
- Stockout Rate: Indicates the frequency of stockouts, helping evaluate demand planning accuracy.
- Carrying Cost of Inventory: Reflects the total cost associated with holding inventory, impacting overall profitability.
- Lead Time: Measures the time taken from order placement to product delivery, influencing procurement strategies.
These metrics provide decision-makers with insights into which software can best enhance operational efficiency and inventory management.
Comparative Data on Leading Software Solutions
An analysis of leading stock planning software solutions showcases varying capabilities. Solutions like NetSuite, SAP Integrated Business Planning, and Microsoft Dynamics 365 offer distinct features tailored to different business needs.
For example, NetSuite is well-known for its user-friendly interface and strong ERP integrations, which streamline operations. On the other hand, SAP Integrated Business Planning is favored for its robust analytics capabilities, making it ideal for larger enterprises with complex needs.
In the following sections, we will delve deeper into methodologies and best practices for stock management, ensuring a comprehensive understanding of effective stock planning strategies.
Understanding Stock Planning
Stock planning is a critical aspect for any organization that deals with inventory. It encompasses strategies and practices designed to manage stock levels effectively. In a world where supply chains face increasing uncertainty and demand fluctuations, understanding stock planning is essential for maintaining operational efficiency.
Effective stock planning enables businesses to align their inventory with customer demand, minimizing the risk of both overstocking and stockouts. Over time, this proactive approach leads to enhanced cash flow and productivity. It fosters relationships with suppliers and strengthens customer satisfaction, as companies can respond effectively to market needs.
When approaching stock planning, several key considerations emerge. Companies must assess their current inventory systems and determine the appropriate stock levels in accordance with their operational goals. Moreover, the integration of advanced analytics and forecasting models plays a significant role in optimizing stock management, making this understanding even more crucial for decision-makers in todayβs technology-driven environment.
Definition and Importance
Stock planning refers to the process of determining the right amount of inventory needed to meet customer demand while minimizing excess stock. Proper stock planning is important for various reasons. First, it helps to maintain an efficient supply chain. Businesses can effectively manage their resources, which leads to lower costs related to storage and obsolescence. Second, proper planning can help identify trends in customer behavior, leading to better sales forecasting and inventory decisions.
In terms of logistics, understanding stock planning impacts delivery schedules and production timelines, ensuring that companies can operate smoothly without interruption. Ultimately, a well-planned inventory strategy is a cornerstone for profitability in both large enterprises and small businesses.
Key Principles of Stock Planning
Effective stock planning is guided by several key principles:
- Demand Forecasting: Accurate demand forecasting is vital. It involves predicting future product demand based on historical data, market trends, and seasonal variations. Companies often use data analytics tools to enhance the accuracy of their forecasts.
- Optimal Reorder Levels: Determining when to reorder stock is essential in stock planning. Companies must identify reorder points that trigger restocking based on lead times and sales velocity.
- Safety Stock: Maintaining a safety stock helps organizations cushion against unexpected demand surges or supply chain delays. This principle minimizes the risk of stockouts while optimizing inventory turnover.
- Continuous Monitoring: The stock planning process is dynamic and requires ongoing evaluation. Regular reviews of inventory performance and market trends enable companies to adapt their strategies in response to changing conditions.
- Collaboration Across Departments: Stock planning should not exist in isolation. Close cooperation between sales, marketing, and supply chain teams maximizes the effectiveness of stock strategies.
By integrating these principles, organizations can develop a robust stock planning framework that enhances decision-making processes and boosts overall efficiency.
Types of Stock Planning
Understanding the various types of stock planning is crucial for any business aiming to optimize its inventory management. Each method offers unique benefits and considerations that can significantly impact how companies manage their stock. Selecting the right type of stock planning can lead to reduced costs, improved efficiency, and ultimately, greater customer satisfaction. Here, we will explore three main types of stock planning: Just-In-Time, Material Requirements Planning, and Demand-Driven MRP. Each of these categories provides different strategies to manage inventory effectively.
Just-In-Time (JIT)
Just-In-Time stock planning focuses on minimizing inventory levels by aligning production schedules closely with demand. This strategy requires accurate demand forecasts and reliable suppliers. As a result, the goal is to reduce waste and carry just enough stock to meet immediate needs.
Benefits of JIT include:
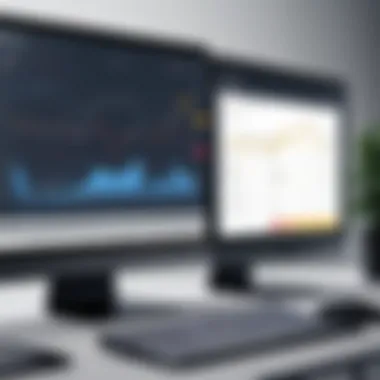
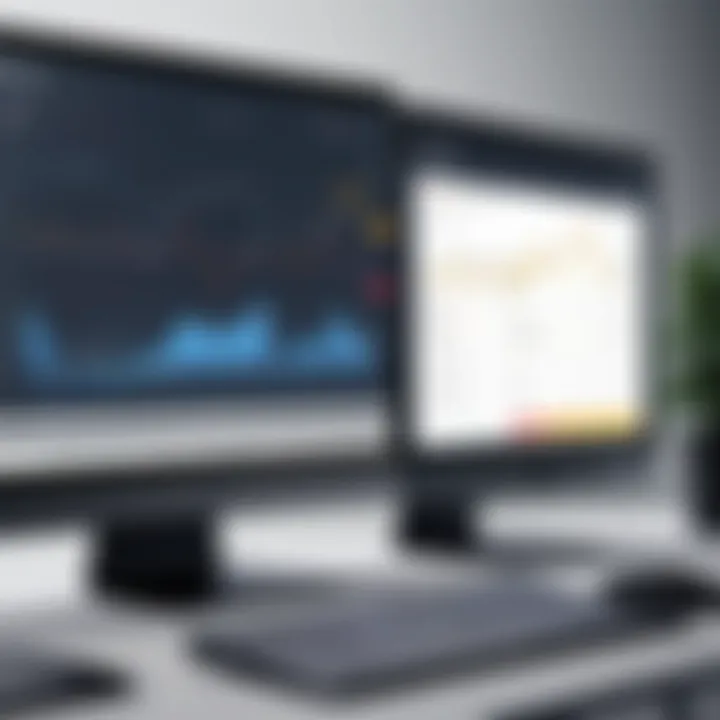
- Reduced holding costs: By keeping stock low, a company can free up capital that would otherwise be tied in unsold inventory.
- Increased efficiency: Lean operations often lead to streamlined processes, allowing businesses to respond quickly to changes in demand.
- Flexibility: JIT enables better adaptability as companies can modify production schedules based on actual demand rather than predictions.
However, JIT also has its drawbacks. For example, any disruption in the supply chain can have serious ramifications. A delay from a supplier or an unexpected increase in demand can lead to stockouts and customer dissatisfaction. Thus, careful planning and reliable supplier relationships are essential for successful implementation.
Material Requirements Planning (MRP)
Material Requirements Planning (MRP) is a system that calculates material needs based on production schedules and customer orders. MRP works backward from a finished product, determining what materials are necessary and when they are needed. This approach allows businesses to maintain optimal inventory levels while ensuring that production processes run smoothly.
Advantages of MRP include:
- Improved inventory management: MRP helps maintain the right amount of stock, leading to decreased waste and reduced carrying costs.
- Enhanced planning: It provides insight into future material needs, helping businesses to better plan their procurement strategies.
- Streamlined production: With accurate material planning, production can occur without delays, enhancing overall throughput.
Despite its strengths, MRP can be complex to implement. It requires robust data inputs and precise forecasts. Inaccurate information can lead to either excessive inventory or shortages.
Demand-Driven MRP (DDMRP)
Demand-Driven MRP (DDMRP) is an evolution of traditional MRP that emphasizes real-time data and actual demand rather than relying solely on forecasts. This methodology adapts to fluctuations in demand, enabling businesses to react swiftly to changing market conditions.
Key features of DDMRP include:
- Buffer management: DDMRP establishes stock buffers at critical points in the supply chain, helping to absorb variability in demand and supply.
- Prioritization of flow: It focuses on the flow of materials rather than just material availability, which optimizes production schedules directly based on actual demand.
- Enhanced visibility: Real-time data analysis facilitates quicker decision-making and improved responsiveness.
The blend of demand-driven principles along with inventory management allows companies to increase service levels and decrease lead times effectively. However, the transition to DDMRP requires training and cultural changes within organizations.
Key Components of Stock Planning
In the realm of stock management, certain components play a critical role in ensuring the entire process functions effectively. These components contribute to optimizing inventory levels, minimizing costs, and streamlining operations. A focused approach on key elements allows organizations to anticipate demand fluctuations, manage supplier relationships, and ultimately enhance efficiency. Understanding these key components is essential for any business aiming to excel in stock planning.
Inventory Management Software
Inventory management software serves as the backbone of modern stock planning. This tool facilitates tracking inventory levels, orders, sales, and deliveries in real time. The benefits of utilizing such software are manifold. Firstly, it automates mundane tasks, reducing human error and freeing personnel for strategic planning. Secondly, it provides detailed insights into inventory turnover rates, helping businesses identify slow-moving stock. Furthermore, many software solutions offer integration with e-commerce platforms and accounting systems, promoting seamless operations across various departments. Choosing the right software necessitates an understanding of the specific needs of the organization. Factors to consider include scalability, user-friendliness, and support options.
"Selecting the appropriate inventory management software can significantly alter the course of stock planning efficacy."
Demand Forecasting Techniques
Effective demand forecasting techniques are indispensable for informed stock planning. Organizations must accurately predict customer demand to avoid stockouts or overstock situations. Several methods can be employed, ranging from qualitative approaches, such as expert opinions and market research, to quantitative methods that utilize historical data and algorithms.
For instance, moving averages and exponential smoothing are commonly practiced quantitative methods. These techniques utilize past sales data to project future demand, thus allowing businesses to make proactive decisions regarding inventory purchases. Advanced approaches include machine learning algorithms that leverage vast datasets to refine predictions further. In addition to techniques, a mixed-method approach often yields the best outcomes as it captures diverse aspects of demand behavior.
Lead Time Analysis
Lead time analysis is another essential element in stock planning. Understanding the time it takes from placing an order to receiving goods is crucial for maintaining optimal inventory levels. Efficient lead time management helps businesses avoid disruptions in the supply chain. Factors affecting lead time can include supplier reliability, shipping methods, and seasonal fluctuations.
By closely monitoring lead times, organizations can adjust their ordering cycles appropriately. This ensures that stock arrives when needed rather than accumulating unnecessary overhead costs. Moreover, maintaining open communication channels with suppliers aids in negotiating better lead times and understanding potential delays. Companies should regularly assess their lead times to implement continual improvement strategies, including performance metrics and supplier evaluations.
Strategies for Effective Stock Planning
Effective stock planning is crucial for any business that relies on inventory. It helps to balance supply with demand, minimizing costs and maximizing profit. Companies that implement effective stock planning strategies can improve their operational efficiency and customer satisfaction. These strategies not only address how much stock to hold but also when and how to replenish it.
Establishing Safety Stock Levels
Setting appropriate safety stock levels is an essential strategy in stock planning. Safety stock acts as a buffer against unforeseen fluctuations in demand. This could include unexpected spikes in orders or delays in supply shipments. Establishing the right safety stock requires careful analysis of past sales data and demand forecasting.
Businesses should factor in the lead time for replenishment and the variability in customer demand. A precise calculation helps prevent stockouts, which can disrupt sales and damage customer trust.
Additionally, businesses should regularly review their safety stock levels. Changes in sales patterns, market conditions, or supplier reliability may necessitate adjustments.
Cycle Counting
Cycle counting is another important strategy in stock planning. Unlike a full inventory audit, cycle counting allows businesses to regularly assess inventory in smaller, manageable portions. This method is beneficial as it identifies discrepancies and reduces the likelihood of significant stock issues go unnoticed.
By implementing a consistent cycle counting schedule, companies can maintain higher accuracy in their inventory records. It also fosters a culture of accountability among employees, ensuring they understand the importance of inventory accuracy. Incorporating technology, such as inventory management software, can streamline the cycle counting process.
Stock Valuation Methods
Properly valuing stock is a critical aspect of effective stock planning. Various methods, like First-In-First-Out (FIFO), Last-In-First-Out (LIFO), and weighted average cost, can be employed. Each method has its merits and may affect financial statements and tax positions differently.
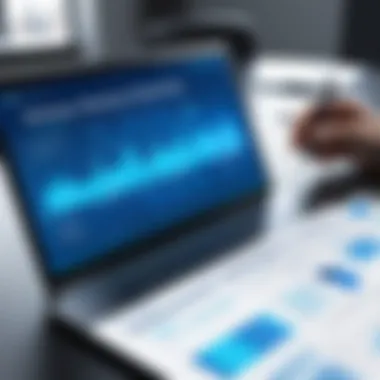
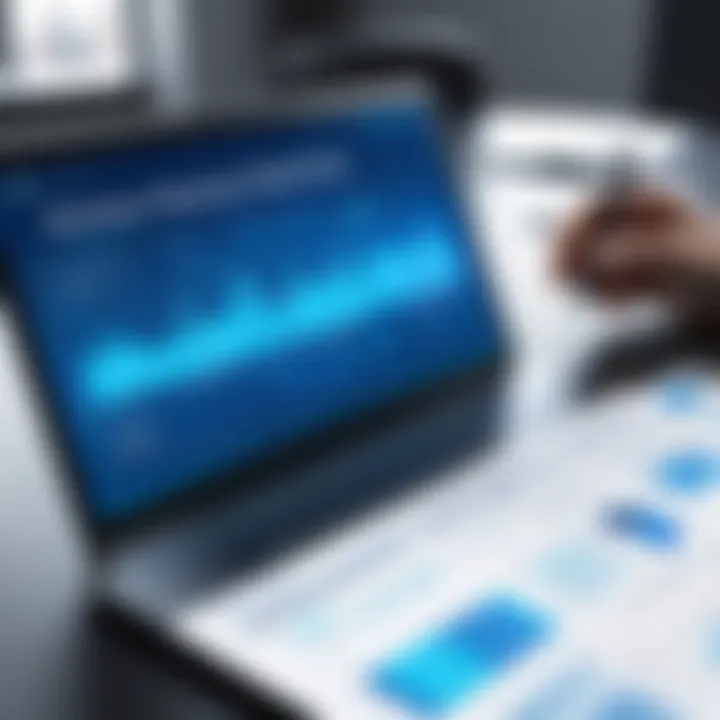
Choosing a valuation method should align with the business's operational needs and financial objectives. For instance, FIFO is commonly used in industries with perishable products, while LIFO might be more beneficial during inflationary periods. Understanding these methods helps businesses make more informed decisions about inventory management, impacting cash flow and profitability.
Maintaining clear visibility over stock valuation methods ensures that businesses can effectively monitor their inventory health and financial performance.
Implementing Stock Planning Tools
Implementing stock planning tools is a crucial step for businesses looking to optimize inventory management. The right tools not only streamline processes but also enhance decision-making capabilities. Effective stock planning tools offer visibility into stock levels, demand forecasts, and supplier performance. This helps organizations maintain appropriate inventory levels, thus preventing stockouts and overstocking situations.
Moreover, with increasing competition and market demands, having insightful data at hand becomes necessary. Developing a framework for successful implementation can vastly improve overall efficiency. Consideration must be given to software capabilities, integration potential, user-friendliness, and support service.
Choosing the Right Software
The choice of software plays a significant role in stock planning. A well-selected program can address unique business needs and facilitate smooth operations. When choosing software, several key factors should be assessed:
- Scalability: The software must adapt as the business grows. It should support additional features or users without extensive upgrades.
- Integration capability: Ability to work seamlessly with existing systems such as ERP, CRM, and accounting software is essential. This ensures consistent data flow across platforms.
- User interface: A clean and intuitive interface minimizes training time and promotes user adoption. A complex system may lead to frustration and errors.
- Cost-effectiveness: Analyze both initial costs and long-term operational expenses. Look for software that offers good return on investment.
In addition, reading user reviews and seeking peer recommendations can provide practical insights into the software's performance.
Integrating Stock Planning Systems
Integration of stock planning systems is pivotal for businesses aiming for streamlined operations. Once the software is selected, it needs to be properly integrated with current systems and processes. This can involve data migration, workflow alignment, and user training. Here are some considerations to ensure a successful integration:
- Assess current systems: Understanding existing systems helps identify compatibility challenges. This will ease transitions and highlight necessary modifications.
- Data synchronization: Ensure stock levels, orders, and supplier details sync across all platforms, preventing discrepancies.
- Training and support: User training is key in leveraging the new systems effectively. Allocate time for hands-on training and assessments to boost confidence among staff.
- Monitor performance: After integration, ongoing assessment of system performance is required. Key performance indicators should be established to measure impact on stock management.
With proper implementation and integration of stock planning tools, businesses can experience enhanced operational efficiency, reduced costs, and improved service levels.
Challenges in Stock Planning
Effective stock planning is crucial for maintaining optimal inventory levels. Nevertheless, several challenges can impede this process, leading to increased costs and inefficiencies. Understanding these challenges allows businesses to devise better strategies and remain competitive. The significance of addressing challenges in stock planning cannot be overstated, as it provides insights into operational performance and influences decision-making.
In this section, we will explore three core challenges faced in stock planning: demand variability, supplier reliability, and inventory holding costs. Each challenge has unique implications for stock management, impacting everything from customer satisfaction to financial performance.
Demand Variability
Demand variability is one of the most prominent challenges in stock planning. It refers to the fluctuations that can affect customer orders based on seasonality, market trends, and economic shifts. Businesses must respond quickly to changes in consumer behavior. Otherwise, they risk overstocking or understocking products.
A few key points about demand variability include:
- Impact on Inventory Levels: Increased demand can lead to stock-outs, while decreased demand can result in excess inventory.
- Forecasting Difficulty: Accurate demand forecasting is complicated due to many external factors.
- Mitigation Strategies: Some companies implement sophisticated demand forecasting techniques to better predict changes in consumer preference.
Companies should recognize that demand variability is not entirely predictable. Therefore, preparing for potential fluctuations through strategic planning is essential.
Supplier Reliability
Supplier reliability is another challenge in stock planning. Reliable suppliers are crucial for maintaining consistent stock levels. Unreliable suppliers can lead to delays, substandard products, or unexpected supply chain disruptions.
Consider the following aspects of supplier reliability:
- Quality Assurance: Regularly assess supplier performance to ensure quality and timeliness.
- Diversifying Suppliers: Working with multiple suppliers reduces the risk of supply interruptions.
- Long-Term Relationships: Collaborating with suppliers fosters trust and encourages better service and priority during crises.
Effective stock planning relies on a dependable network of suppliers. Establishing solid relationships and consistently monitoring supplier performance can help companies mitigate this challenge.
Inventory Holding Costs
Inventory holding costs involve expenses linked to storing unsold goods. These costs can quickly accumulate and significantly affect a business's bottom line. Balancing inventory levels to minimize holding costs without jeopardizing product availability is a delicate act.
Understanding inventory holding costs is essential for effective stock management. Here are key components:
- Storage Expenses: Costs related to warehousing and facilities.
- Obsolescence: The risk that products may become outdated or unsellable.
- Capital Costs: Tied-up capital that could otherwise invest in growth initiatives.
- Insurance and Taxes: Additional expenses related to maintaining inventory.
To reduce holding costs, businesses should strive to optimize inventory turnover rates and embrace just-in-time methodologies where feasible. Adjusting stock levels quickly in response to demand can also lead to reduced holding costs.
Maintaining optimal stock levels is a balancing act. Failure to address these challenges can lead to financial losses and subpar customer satisfaction.
Data Analytics in Stock Management
In the context of stock management, data analytics has emerged as a crucial tool. Its significance lies in the ability to transform vast amounts of raw data into actionable insights. Businesses today generate data from various sources, including sales transactions, customer preferences, and market trends.
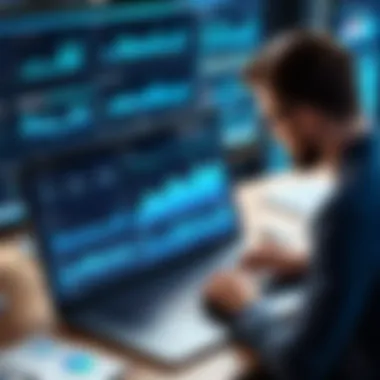
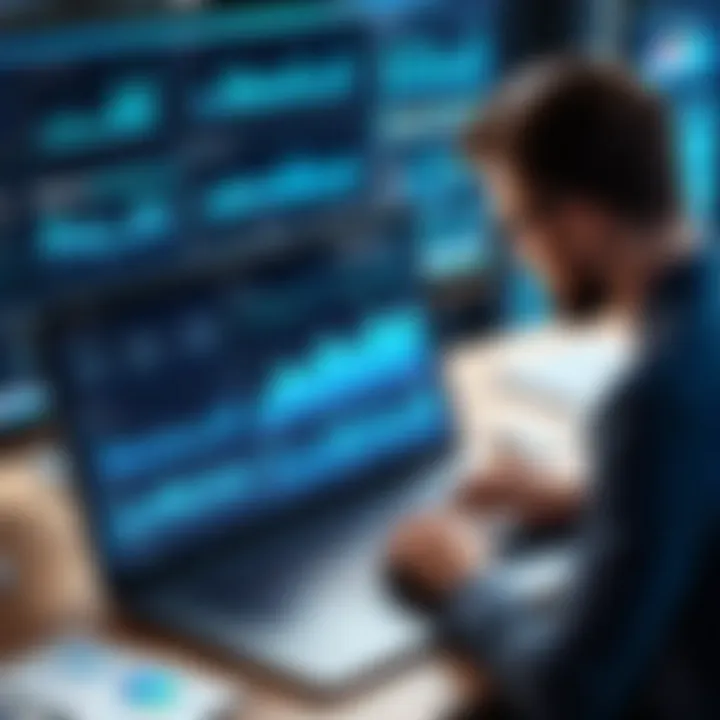
By applying data analytics, managers can optimize inventory levels, reduce waste, and enhance overall efficiency. This approach allows for a better understanding of purchasing patterns and demand fluctuations. The integration of data analytics enables companies to maintain a competitive edge in a fast-paced market.
Role of Data in Stock Planning
Data plays a pivotal role in stock planning. Accurate data collection is essential for effective inventory management. It allows businesses to predict future demand more reliably. For instance, historical sales data can indicate seasonal trends and help firms prepare accordingly.
Moreover, real-time data enhances responsiveness to market changes. If a sudden spike in demand occurs, immediate data analysis can inform necessary adjustments in stock levels. Key performance indicators (KPIs) can also be monitored effortlessly, providing a concise overview of inventory health. Therefore, investing in relevant data collection methods becomes vital for precise stock planning.
"Data is a precious thing and will last longer than the systems themselves."
Data-Driven Decision Making
Data-driven decision-making represents a systematic approach that relies on data analysis to inform business choices. In stock management, this method can significantly enhance operational efficiency. Companies that leverage data can minimize inventory costs and improve order fulfillment rates.
By embracing data analytics, decision-makers can address challenges proactively. For example, advanced forecasting models can help anticipate potential stock-outs or overstocks. By integrating this intelligence into their processes, firms can create a balance that accommodates varying demand levels.
In addition, adopting a data-centric culture fosters collaboration among departments. Sales, marketing, and inventory management teams can work together using shared insights. This unified approach aids in driving effectiveness across stock planning initiatives. Furthermore, continuous learning from past data enhances future strategy formulation, creating a cycle of improvement.
Case Studies on Stock Planning
Understanding case studies on stock planning is crucial for anyone engaged in the realm of inventory management. These case studies serve as pragmatic examples, illuminating both the successful implementations and the pitfalls businesses often encounter. They provide tangible insights that theoretical frameworks alone may lack. Moreover, examining real-world examples allows for a more nuanced understanding of strategic application, operational efficiency, and decision-making frameworks involved in stock planning.
The benefits of engaging with case studies in stock planning can be wide-ranging:
- Real-World Applications: They showcase how various companies have applied stock planning methodologies, offering actionable insights for businesses of all sizes.
- Lessons from Experience: Analyzing failures reveals common mistakes and offers guidance on avoiding them, thereby improving future planning strategies.
- Benchmarking: Successful examples provide a benchmark for performance, enabling companies to evaluate their strategies against leading practices in the industry.
- Adaptation of Best Practices: Businesses can adapt successful practices from different industries or contexts to their specific needs and operations.
By utilizing case studies, professionals can enhance their understanding of stock planning, ultimately aiding in better decision-making and planning outcomes. The next sections focus on examples of successful implementations and lessons learned from failures, providing an in-depth view of the landscape of stock planning.
Successful Implementation Examples
Numerous companies across diverse industries have effectively implemented stock planning strategies, leading to significant improvements in efficiency and cost management. For instance, a prominent automotive manufacturer adopted a Just-In-Time (JIT) approach coupled with advanced inventory management software.
This integration allowed them to minimize excess inventory while meeting production demands promptly. They reported a 25% reduction in inventory holding costs alongside an improved production timeline. Their success hinged on the following factors:
- Clear Objectives: Defining goals before implementation enabled targeted strategies.
- Effective Communication: Engaging all stakeholders ensured alignment within the organization.
- Continuous Monitoring: Regular assessments of performance metrics allowed for quick adjustments and optimization.
- Training: Staff training ensured that all team members could effectively use new systems and operate them efficiently, reducing errors.
Another example can be seen in a large retail chain that utilized demand forecasting techniques to tailor their stock levels more accurately. By leveraging historical sales data and seasonal trends, they optimized their ordering processes, resulting in a 30% decrease in stockouts and increased customer satisfaction.
Lessons Learned from Failures
While success stories are impactful, learning from failures in stock planning can be equally instructive. Companies that disregard thorough planning can fall victim to increased costs and diminished operational efficiency. An instance of this is a major electronics retailer that faced severe overstock issues due to poor demand forecasting.
The repercussions included:
- Increased Holding Costs: Excess stock tied up capital, leading to cash flow constraints.
- Obsolescence Risks: Technology products became outdated quickly, resulting in hefty markdowns to clear stock.
- Diminished Market Reputation: Customers became frustrated with reduced product availability due to mismanaged inventory cycles.
Key lessons from this failure include:
- Importance of Accurate Forecasting: Utilizing robust demand forecasting methods is essential for maintaining optimal inventory levels.
- Integration of Systems: A lack of integration between sales data and inventory management led to mismatched stock levels, emphasizing the need for cohesive systems.
- Flexibility: Businesses must remain adaptable to changing trends and market demands; rigidity can lead to significant losses.
The Future of Stock Planning
The future of stock planning is evolving rapidly, reflecting changes in technology, consumer behavior, and global markets. This article emphasizes the importance of understanding and adapting to these shifts. By recognizing emerging technologies and trends, businesses can enhance their inventory management practices and maintain a competitive edge. Effective stock planning will increasingly rely on data analytics and automation, requiring professionals to stay informed and agile.
Emerging Technologies
Emerging technologies are transforming the landscape of stock planning. Automation is at the forefront, with systems that streamline ordering processes and inventory tracking. For example:
- Artificial Intelligence: AI algorithms provide predictive analytics, enabling companies to forecast demand with greater accuracy. This technology helps in adjusting stock levels proactively, reducing the risk of overstocking or stockouts.
- Internet of Things (IoT): IoT devices facilitate real-time inventory monitoring. Sensors in warehouses can track product levels and send alerts when inventory reaches critical points. This leads to increased efficiency and minimizes manual errors.
- Blockchain Technology: Blockchain offers transparency in supply chain management. It enhances traceability of goods, reducing counterfeits and ensuring compliance with regulations. Companies can track product journeys from suppliers to customers seamlessly.
Businesses that embrace these technologies can achieve notable benefits, including reduced costs, improved accuracy, and enhanced agility in responding to market demands.
Trends in Inventory Management
Several trends are shaping the future of inventory management:
- Sustainability Practices: Companies are increasingly focusing on sustainability. Stock planning must now consider environmental impact. Efficient resource use and minimizing waste are becoming central to inventory strategies.
- Customization and Personalization: As consumers demand more tailored experiences, businesses need to adjust stock planning to accommodate varied customer preferences. This requires effective management of both standard inventory and customized orders.
- Omnichannel Retailing: The rise of online shopping demands a cohesive stock strategy across multiple channels. Customers expect seamless service, whether purchasing in-store or online. Thus, integrating inventory planning across all platforms is essential.
Adjustments to stock planning will not only improve business processes but also enhance customer satisfaction and loyalty.
In summary, the future of stock planning is driven by technology and collaboration, fundamentally changing how businesses manage inventory.
Technological advancements paired with evolving market trends mean that continuous education and adaptability will be crucial for professionals in the field.