Understanding Inventory Process Flow for Businesses
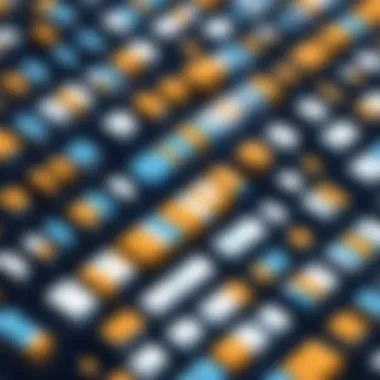
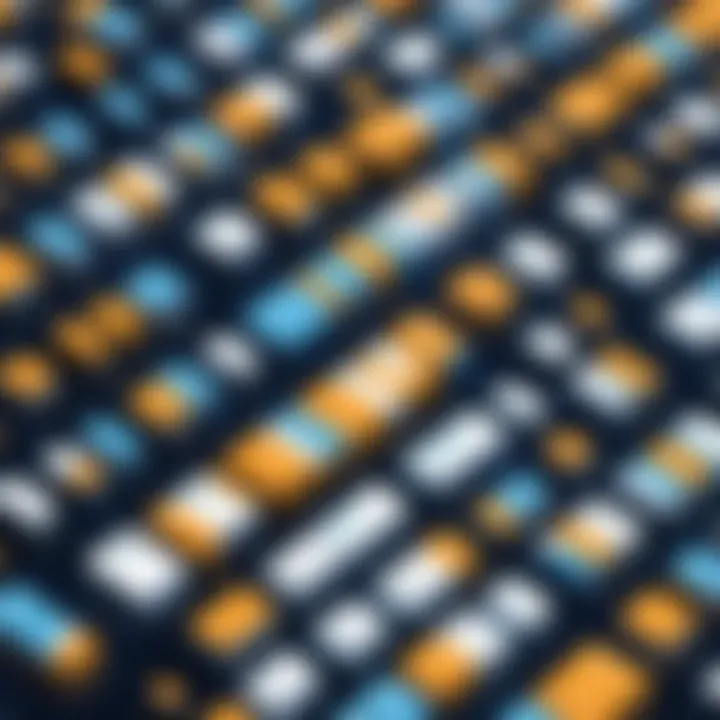
Intro
In the realm of business operations, understanding the inventory process flow is crucial for achieving efficiency and maximizing profitability. This subject encompasses various stages, from the procurement of goods to their final sale. Companies strive for optimized inventory management to balance their supply with customer demand. This article aims to explore the individual components of inventory process flow and their significance within diverse operational frameworks.
As we navigate through the complexities of inventory management, we will uncover best practices and common challenges encountered by businesses. Additionally, we focus on data-driven approaches, which help decision-makers implement strategies that enhance oversight and logistics.
Software Category Overview
Purpose and Importance
Software solutions play an essential role in managing inventory effectively. These tools assist businesses in tracking stock levels, orders, sales, and deliveries, providing a seamless flow of information. The purpose of such software is to ensure that the right products are available at the right time, thereby reducing costs associated with overstocking and stockouts.
The importance of inventory management software cannot be overstated. It affects cash flow, customer satisfaction, and overall operational efficiency. Companies that prioritize this aspect of their operations typically enjoy a competitive edge in their respective markets.
Current Trends in the Software Category
The landscape of inventory management software is continually evolving, driven by technological advancements. Current trends include:
- Cloud-based solutions: They offer flexibility and accessibility for remote inventory tracking and management.
- Artificial Intelligence and Machine Learning: These technologies enable more accurate demand forecasting and reduce human errors.
- Integration with other systems: Businesses increasingly seek software that can seamlessly connect with ERP and CRM systems to streamline overall operations.
These trends reflect a shift towards more sophisticated, scalable solutions that can adapt to the ever-changing demands of the market.
Data-Driven Analysis
Metrics and Criteria for Evaluation
When evaluating inventory management software, several metrics are critical. These include:
- Inventory Turnover Ratio: This indicates how many times inventory is sold and replaced over a period.
- Carrying Costs: The costs associated with holding unsold goods.
- Forecast Accuracy: Measures how well the software predicts future inventory needs.
- Lead Times: The time it takes from ordering a product to having it available for sale.
Assessing these metrics allows businesses to determine the efficacy of their inventory management strategies.
Comparative Data on Leading Software Solutions
In today's market, numerous inventory management software solutions exist, each with unique features and capabilities. When comparing leading options such as TradeGecko, NetSuite, and Cin7, businesses should consider:
- User Interface: An intuitive layout can significantly enhance usability.
- Integration Options: Compatibility with existing systems is vital for smooth operations.
- Pricing Structure: Cost plays a pivotal role in decision-making.
- Customer Support: Access to reliable support services is essential for troubleshooting issues.
Understanding these comparisons can guide businesses in choosing the right software tailored to their specific needs.
"Effective inventory management is not just about stock; it shapes the core of a business's operational effectiveness, influencing overall strategy and customer satisfaction."
Ultimately, appreciating the nuances of inventory process flow empowers decision-makers to optimize their operations while adapting to ever-evolving market conditions.
Preamble to Inventory Process Flow
Inventory process flow is a crucial aspect of supply chain management and operational efficiency. It encompasses every movement of inventory from procurement to storage, and eventually to sale. Understanding this flow can dramatically enhance a business’s ability to meet consumer demand, manage costs, and utilize resources effectively.
By grasping the complexities of inventory process flow, organizations can identify inefficiencies and seize opportunities to optimize their operations. This knowledge is essential for tech-savvy individuals, business professionals, and IT experts seeking to enhance overall effectiveness in their respective fields.
Definition of Inventory Process Flow
Inventory process flow refers to the systematic sequence through which inventory moves within an organization. It starts with the selection of suppliers and moves through procurement, receiving, storing, and eventually fulfilling customer orders. Each stage of this flow can significantly impact service levels, operational costs, and ultimately profitability.
The flow can be divided into specific stages:
- Stock Procurement: Involves selecting suppliers, placing orders, and managing costs.
- Receiving Inventory: Includes inspecting the inventory received, ensuring proper documentation, and stock identification.
- Inventory Storage: Dictates how inventory is organized and maintained within the storage facilities.
This structured process is vital for businesses of all sizes, ensuring that the right products are available at the right time.
Importance of Effective Inventory Management
Effective inventory management is paramount for thriving in today’s competitive market. Its importance stretches across several domains:
- Cost Control: Poor inventory management can lead to overstocking or stockouts, both of which incur unnecessary costs. Proper management allows businesses to maintain optimal stock levels, minimizing carrying costs.
- Customer Satisfaction: Timely fulfillment of customer orders hinges on a well-managed inventory. Customers expect products to be available when they need them, and effective inventory management plays a key role in meeting these expectations.
- Data Accuracy: Accurate inventory records reduce discrepancies between physical stock and recorded inventory, enhancing decision-making processes.
- Adaptability: A sound inventory management strategy allows businesses to adapt quickly to market changes or unforeseen events.
The essence of successful inventory management is not merely in tracking stock; rather, it embodies a comprehensive approach to resource consolidation and operational excellence.
Key Components of Inventory Process Flow
Understanding the key components of inventory process flow is essential for businesses aiming to streamline their operations. Each part of this flow contributes to effective inventory management, impacting overall efficiency and profitability. By analyzing the various elements involved, organizations can identify potential improvements, reduce costs, and enhance customer satisfaction.
Stock Procurement
Stock procurement is the initial step in acquiring inventory. It involves sourcing and obtaining products or materials necessary for business operations. Effective procurement helps maintain a balance between supply and demand, minimizing both excess inventory and shortages.
Supplier Selection
Supplier selection is crucial for ensuring quality and reliability in inventory procurement. Choosing the right supplier can significantly influence costs and product availability. Key characteristics of effective supplier selection include evaluating the supplier’s track record, financial stability, and delivery capabilities.
This aspect is beneficial as it reduces risks associated with delays and poor-quality goods. However, the challenge lies in thoroughly vetting potential suppliers, which can be time-consuming. A unique feature of supplier selection involves establishing long-term partnerships instead of one-time agreements, which can enhance trust and mutual benefits over time.
Order Placement Strategies
Order placement strategies dictate how and when inventory is ordered from suppliers. These methodologies play a vital role in managing cash flow and ensuring smooth operations. A popular choice for order placement is Just-in-Time (JIT) ordering, which minimizes inventory holding costs.
The advantage of JIT is that it optimizes warehouse space and improves cash flow. However, it can also lead to stockouts if supply chain disruptions occur. Another approach is bulk ordering, which can yield discounts but may lead to excess inventory. Balancing these strategies is critical to maintaining an effective inventory system.
Cost Considerations
Cost considerations encompass all financial aspects associated with inventory procurement. Analyzing the costs involved—such as purchase price, shipping fees, and potential holding costs—can provide insights into the overall effectiveness of procurement strategies.
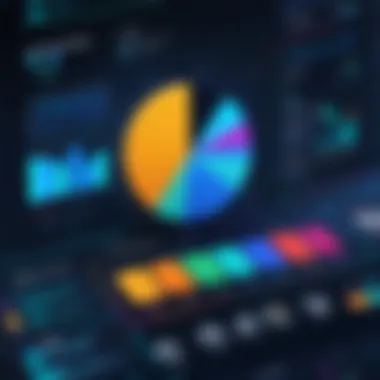
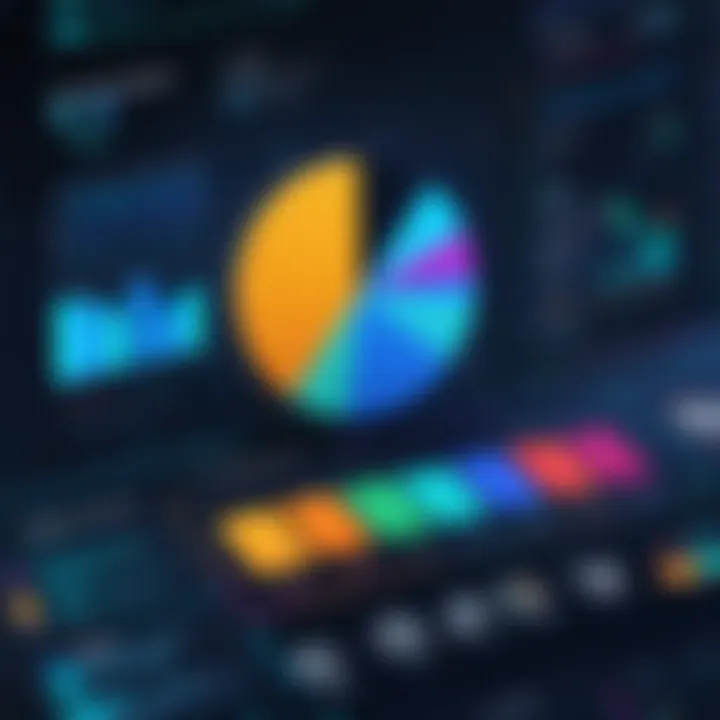
A noteworthy characteristic of cost considerations is understanding the total cost of ownership, which includes not just the initial purchase price but also ongoing expenses incurred throughout the product’s lifecycle. It is beneficial because this comprehensive view can guide better procurement decisions. However, the complexity of accurately estimating these costs can be a downfall for many businesses.
Receiving Inventory
Receiving inventory is the process of accepting goods once they arrive at the facility. This stage is pivotal for quality control and inventory accuracy. Properly managing this phase ensures that inventory levels reflect actual stock on hand, which is crucial for effective inventory management.
Inspection Procedures
Inspection procedures involve checking the quality and condition of items received. This process prevents defective goods from being added to inventory, ensuring quality control. A key point of these procedures is adhering to predefined quality standards and specifications.
This practice can be advantageous in upholding a company's reputation for quality. However, it may slow down the receiving process if not streamlined properly. Unique to this aspect, companies often implement automated inspection systems that speed up these procedures while maintaining accuracy.
Documentation Requirements
Documentation requirements entail the necessary paperwork and records associated with inventory receipts. Each shipment must be documented to maintain accountability and track inventory movements accurately. Significant characteristics include maintaining invoices, packing slips, and delivery receipts.
This is vital for ensuring that received quantities match ordered amounts. The complexity of documentation can rise, leading to administrative challenges, especially for larger organizations. Adopting digital documentation can simplify this process, reducing risks of errors and improving accessibility.
Stock Identification
Stock identification focuses on categorizing and labeling received inventory. Proper stock identification is crucial for efficient inventory management and quick retrieval. The key element of stock identification is implementing systems such as barcode labeling or RFID tracking.
This practice enhances traceability and efficiency in stock handling. Nonetheless, setting up these systems requires an initial investment that some may find daunting. A unique facet of stock identification is that it supports real-time inventory tracking, allowing for more accurate forecasting and planning.
Inventory Storage Techniques
Efficient inventory storage techniques are essential for maximizing space and ensuring easy access to products. How companies store their inventory affects retrieval times, organization, and ultimately, the bottom line.
Storage Systems Overview
Storage systems overview describes the various methods and equipment used for storing inventory. Common options include pallet racks, shelving, and automated storage systems. A significant characteristic involves assessing space availability and inventory turnover rates.
This is beneficial as optimized storage can lead to more efficient operations and improved space utilization. On the downside, the initial setup costs can be high, particularly for automated systems. Understanding specific storage needs enables businesses to select the most appropriate solution.
Space Optimization Strategies
Space optimization strategies are techniques aimed at utilizing warehouse space effectively. Adopting best practices such as vertical storage and modular shelving can increase storage capacity. A notable feature of these strategies is their focus on maximizing usable space without extensive renovations.
These strategies are popular because they lead to increased efficiency and reduced costs. However, businesses must regularly evaluate their inventory needs to ensure ongoing effectiveness. Additionally, seasonal fluctuations may require temporary adjustments, adding complexity.
Environmental Control Factors
Environmental control factors address the conditions under which inventory is stored. Factors like temperature, humidity, and light exposure can significantly affect product quality and longevity. Key characteristics include establishing controlled environments when storing sensitive items.
This consideration is essential for industry compliance and preserving product integrity. The challenge lies in the cost and resources required to maintain such environments. However, safeguarding products in this way can prevent losses and add long-term value.
Inventory Management Practices
Inventory management practices are crucial for optimizing the flow of goods within any business. This section emphasizes their role in enhancing efficiency, reducing costs, and improving overall service levels. Effective inventory management practices contribute directly to a company's bottom line by ensuring that the right amount of stock is available at the right time. These practices can reduce waste and enhance customer satisfaction.
Inventory Tracking Methods
Inventory tracking methods are essential for maintaining accurate records and managing stock levels. It allows businesses to monitor supplies, reduce loss, and streamline the process.
Barcode Systems
Barcode systems utilize printed barcodes that are scanned to record inventory movements. This method simplifies the tracking of products and enhances accuracy. The key characteristic of barcode systems is their efficiency in updating inventory records in real time. Barcode systems are beneficial for businesses of various sizes due to their ease of implementation and low cost. A unique feature of barcode systems is that they require minimal training for employees. However, some disadvantages include reliance on physical labels and the need for scanning equipment.
RFID Technology
RFID technology uses electromagnetic fields to automatically identify and track tags attached to objects. The key feature here is the ability to read multiple items at once without a direct line of sight. RFID technology is becoming popular due to its high accuracy and ability to enhance inventory visibility. One unique advantage is its capacity to automate many tasks. However, the technology can be expensive and may require significant initial investment.
Manual Tracking Challenges
Manual tracking involves keeping records by hand or using basic digital tools. The challenge lies in the time-consuming and error-prone nature of this method. A key characteristic of manual tracking is that it often relies on human input, which can lead to inaccuracies. Many small businesses still utilize this method for simplicity and low cost. The unique feature of manual tracking is its straightforward implementation, but its disadvantages include lack of scalability and difficulty in accessing real-time data.
Stock Valuation Techniques
Understanding stock valuation techniques is crucial for determining how inventory impacts financial performance. It helps businesses evaluate their inventory costs more effectively.
FIFO vs. LIFO
FIFO (First In, First Out) and LIFO (Last In, First Out) are methods of inventory valuation that serve different financial strategies. FIFO assumes that the oldest inventory items are sold first, while LIFO accounts for the newest items being sold first. The key characteristic of FIFO is its impact on cash flow and profitability during inflation. Conversely, LIFO can offer tax advantages during periods of rising prices. Each method has unique advantages, including inventory management alignment with cash flow needs and potential impacts on financial reporting.
Weighted Average Cost
Weighted Average Cost evaluates inventory by averaging the cost of all items over a certain period. The key aspect is its straightforward approach to cost calculation. This method provides simplicity and smoothes out price fluctuations. However, it may not reflect current market conditions, leading to inaccuracies in profit margins.
Specific Identification
Specific Identification tracks each inventory item based on its actual cost. The key characteristic of this method is its accuracy, especially for expensive items. This method is particularly beneficial for businesses dealing in high-value or unique items. However, its drawback is impracticality for larger inventories, as it requires detailed record-keeping.
"Effective inventory management practices are not just about maintaining stock levels; they are about understanding the true value of what you hold."
Implementing the right inventory management practices can lead to improved operational efficiency and contribute significantly to the overall success of a business.
Assessing Inventory Performance
Assessing inventory performance is crucial to understanding how well an organization manages its stock. This involves examining key metrics that reveal the efficiency and effectiveness of inventory strategies. With accurate assessments, businesses can make informed decisions that lead to optimized operations and improved profitability. The right tools and methods enhance visibility, helping companies to adapt to market trends and consumer needs.
Key Performance Indicators
To assess inventory performance, several key performance indicators (KPIs) are of significance. They provide insight into the operational health of inventory management.
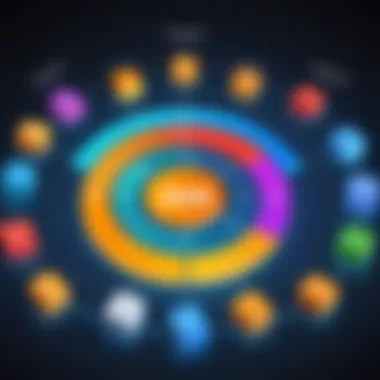
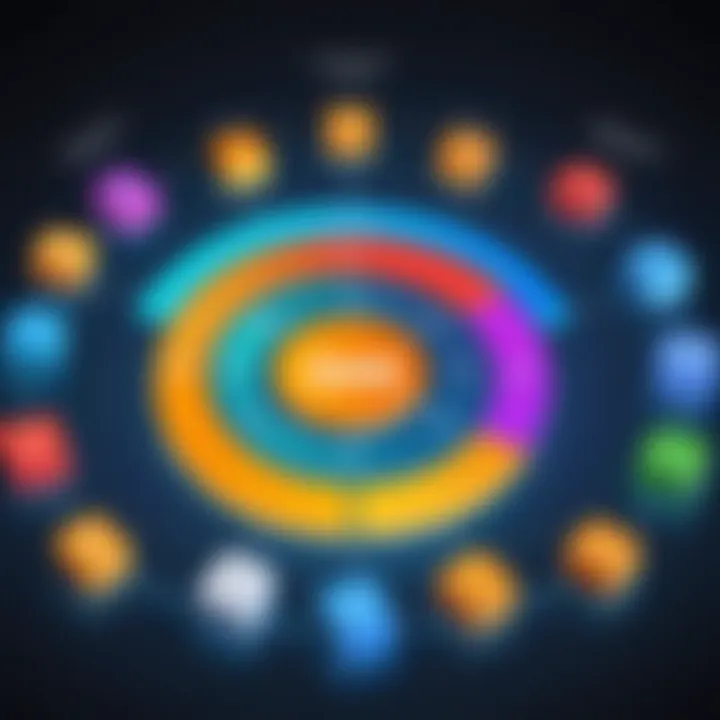
Inventory Turnover Ratio
The Inventory Turnover Ratio reflects how often a company sells and replaces its stock within a specific timeframe. This metric is critical because it indicates sales efficiency. A higher ratio suggests strong sales and effective inventory management. Conversely, a low turnover ratio may point to overstocking or weak sales.
This ratio is particularly beneficial for businesses focusing on aligning inventory levels with customer demand. A unique feature of this indicator is that it can be calculated quite simply using the formula:
When calculated diligently, this can reveal trends that might otherwise go unnoticed. It also helps identify products that are selling slowly, allowing for timely interventions.
Days Sales of Inventory
Days Sales of Inventory measures the average number of days items remain in stock before being sold. This metric factors into cash flow management, with fewer days generally indicating better efficiency. A sharp focus on this KPI is essential because it directly impacts working capital.
The unique feature of this indicator is that it integrates with cash flow forecasts. Therefore, companies looking to improve liquidity often rely on it. However, too few days may indicate stockouts, which can lead to lost sales and customer dissatisfaction.
Stockout Rates
Stockout Rates quantify how often stock is not available when a customer seeks it. This KPI is crucial, as selling opportunities can be lost due to inadequacies in supply chain planning. High stockout rates can reflect inefficient inventory management and mapping.
The key characteristic of this metric is that it acts as a warning signal to management. It suggests required adjustments in ordering or stock levels. However, while low stockout rates are desirable, maintaining a balance between supply and demand is essential—it seems favorable to avoid overstocking as well.
Analyzing Inventory Costs
Understanding inventory costs is another layer of assessing performance. Inventory expenses encompass various aspects, such as carrying costs and order costs, each having far-reaching consequences on profit margins.
Carrying Costs
Carrying Costs represent the total expenses incurred by holding inventory. These include storage fees, insurance, and depreciation. Keeping these costs low is crucial for financial health, as they can accumulate quickly.
The uniqueness of carrying costs is that they directly affect pricing strategies. Companies that effectively manage these costs can offer more competitive pricing and enhance margins. However, if not managed well, these costs can erode profitability.
Order Costs
Order Costs involve expenses associated with acquiring inventory, including shipping and handling. Given that these costs can fluctuate, they require careful monitoring. Ultimately, minimizing order costs can lead to more favorable budget management.
The distinct feature of this metric is its relationship with economic order quantity (EOQ), which helps businesses find the optimal size of inventory orders. Conversely, if not controlled, high order costs can lead to increased financial strain.
Stockout Costs
Stockout Costs represent the lost revenue and negative customer experiences resulting from running out of products. These costs are often underestimated, yet they can severely impact sales performance.
This metric's key characteristic is its potential to affect brand reputation. A history of stockouts may lead to customers opting for competitors. Understanding stockout costs encourages proactive planning and optimal stock levels, ultimately fostering customer loyalty and satisfaction.
Evaluating inventory performance through KPIs and costs gives companies a holistic view of their operations. Better performance leads to improved customer satisfaction, making it an essential aspect of successful inventory management.
Technology in Inventory Management
Technology plays a crucial role in modern inventory management. By leveraging various technological tools and systems, businesses can streamline their processes, improve accuracy, and enhance decision-making. Understanding how technology integrates into inventory processes is essential for any organization aiming to optimize its operations and reduce costs. From software solutions to automation technologies, the integration of these innovations results in more efficient management of stock and resources.
Software Solutions
Cloud-Based Systems
Cloud-based systems have transformed the way inventory is managed. These systems allow users to access data from anywhere at any time. This flexibility is a key characteristic making cloud solutions very popular. Companies can track inventory levels, sales, and orders in real-time without the limitations of traditional systems.
An important feature of cloud-based systems is their scalability. Businesses can easily adjust their services as their needs grow or change. However, there are potential downsides, such as reliance on internet connectivity and concerns around data security, which companies should carefully consider.
Integrating ERP Solutions
Integrating Enterprise Resource Planning (ERP) solutions is another effective strategy in inventory management. ERP systems combine various processes to improve efficiency across departments. This level of integration allows for better coordination between inventory management and other functions, such as accounting and sales.
A notable feature of ERP solutions is their ability to centralize data. This centralization helps minimize data silos and enhances reporting accuracy. Yet, the implementation of ERP can be resource-intensive and requires careful planning and management to address potential disruptions during the transition.
Custom Software Development
Custom software development focuses on creating tailored solutions specific to an organization's inventory management needs. This adaptability is a significant characteristic, enabling organizations to build systems that fit their unique processes and workflows.
The unique feature of custom software is that it can integrate specific functionalities requested by the organization. While this can lead to improved efficiency tailored to the exact needs, it often requires significant financial investment and time for development, as well as ongoing maintenance.
Automation and Inventory Control
Automation in inventory management involves using technology to carry out tasks with minimal human intervention. It plays a vital role in enhancing inventory accuracy and efficiency.
Robotic Process Automation
Robotic Process Automation (RPA) automates repetitive inventory tasks, which helps reduce human error and increases speed. A key characteristic of RPA is its ability to work alongside existing systems without the need for major changes, making it a beneficial option.
A major advantage of RPA is that it allows employees to focus on more strategic tasks rather than mundane operations. However, organizations need to consider the cost of implementation and the change management involved while integrating these systems.
Automated Reordering
Automated reordering systems facilitate the automatic placement of orders when stock levels reach predetermined thresholds. This feature is important for maintaining optimal inventory levels without manual input, ensuring that stockouts are minimized.
The benefit of this automated process is its efficiency, as it reduces manual tracking and helps avoid overstocking. On the downside, it may require precise configuration to ensure the threshold settings effectively meet business needs
Data Analytics Applications
Data analytics applications provide insights into inventory performance, helping businesses make informed decisions about stock levels and ordering strategies. A key characteristic of these applications is their ability to analyze large volumes of data efficiently, identifying trends and patterns.
Data analytics enable proactive inventory management, leading to better forecasting and planning. However, businesses must be wary of relying too heavily on data without a thorough understanding of context, as misinterpretation can lead to poor decision-making.
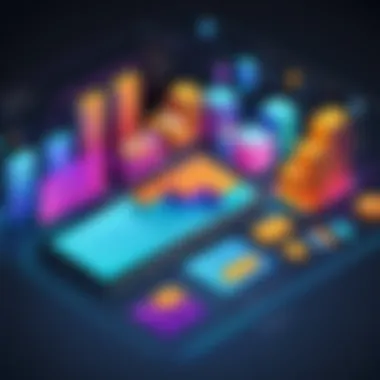
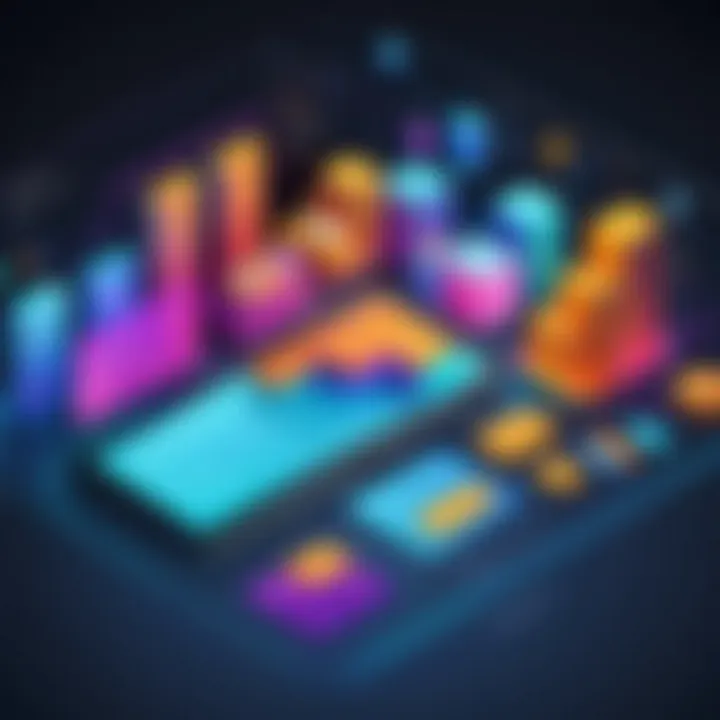
Utilizing technology in inventory management fosters efficiency, enhances accuracy, and enables informed decision-making, which ultimately drives operational success.
Challenges in Inventory Process Flow
Efficient inventory process flow is crucial for businesses to maintain their competitive edge. However, various challenges can disrupt this flow, leading to inefficiencies and increased costs. Understanding these challenges can help businesses develop strategies to mitigate risks and improve inventory management processes.
Common Pitfalls
Overstocking Issues
Overstocking presents a significant challenge in inventory management. It occurs when a business holds more stock than necessary to meet customer demand. This approach can have several drawbacks. First, it ties up capital that could be used for other investments. Second, excess inventory incurs additional costs related to storage and handling. In addition, it may lead to obsolete products that cannot be sold. This issue emphasizes the need for accurate demand forecasting to achieve a balanced inventory level.
Stockout Challenges
Stockouts happen when items are unavailable for sale, often leading to lost sales and disappointed customers. This challenge directly impacts customer satisfaction and can lead to long-term damage to a brand’s reputation. The unpredictability of demand and delays in replenishment are key contributors to stockouts. Businesses must pay close attention to their inventory levels and supplier lead times. Ignoring this can severely disrupt sales channels and overall cash flow.
Data Inaccuracy
Data inaccuracy occurs when inventory records do not reflect actual stock levels. This can arise from various factors, including human error or inadequate tracking systems. Its impact on decision-making can be profound. If a business relies on inaccurate data, it may overorder, underorder, or fail to recognize theft or damage. Thus, maintaining accurate inventory records is fundamentally important, requiring robust processes and regular checks to ensure reliability.
Mitigating Risks
Best Practices for Risk Assessment
Conducting risk assessment is vital for identifying potential inventory-related challenges. Businesses should establish clear criteria for evaluating risks associated with their inventory processes. Regular reviews of suppliers and inventory levels can help uncover vulnerabilities in the supply chain. This proactive approach allows businesses to deploy resources effectively, minimizing potential disruptions.
Developing Contingency Plans
Having contingency plans is essential. These plans prepare a business for unexpected challenges in the inventory process flow, such as sudden increases in demand or supply chain disruptions. By developing clear strategies to address these situations, businesses can maintain operational continuity. Implementing such plans represents foresight that can save time and resources in times of emergency.
Regular Audit Procedures
Regular audits of inventory help ensure accuracy and compliance with inventory management practices. These audits reveal discrepancies in stock levels and can prompt necessary corrective measures. They also confirm that processes are being followed and identify areas for improvement. Businesses that commit to consistent audits can enhance their inventory oversight and reduce the risk of errors and inefficiencies.
Future Trends in Inventory Management
Inventory management is continuously evolving. As businesses strive for efficiency, staying abreast of trends is critical. This section will explore how inventory management is shifting in response to societal expectations and market demands.
Sustainability Considerations
Eco-Friendly Practices
Eco-friendly practices are becoming essential in inventory management. These practices focus on reducing environmental impact while maintaining operational efficiency. One key characteristic of eco-friendly practices is their emphasis on sustainability; they often lead to lower energy costs and improved public perception. By choosing eco-friendly materials and processes, businesses not only meet regulatory requirements but also appeal to a growing consumer base that values sustainability.
The unique feature of eco-friendly practices is their long-term cost savings. Despite initial investments being higher, the reduced energy consumption and waste can lead to significant savings over time. On the downside, these practices may require a robust initial training program to educate employees about new protocols and environmentally friendly materials.
Reducing Waste
Reducing waste is another crucial aspect of modern inventory management. This practice aligns with the overarching goal of achieving operational efficiency while minimizing environmental impact. The focus on waste reduction is beneficial because it often leads to lower costs and increased profit margins. Streamlined processes can also enhance productivity.
A significant unique feature of waste reduction is the application of lean inventory principles. These principles help businesses eliminate excess and unnecessary resources, leading to cost efficiency. However, some businesses may find it challenging to maintain reduced waste levels consistently due to fluctuating market demands.
Green Supply Chain Management
Green supply chain management embodies the concept of sustainability within the broader inventory process. This framework emphasizes reducing the carbon footprint throughout all supply chain stages. A key characteristic of green supply chain management is its holistic approach, integrating suppliers into eco-friendly practices.
The unique advantage of green supply chain management is the potential for enhanced brand loyalty. Consumers increasingly favor businesses that prioritize sustainability. Nonetheless, this approach can lead to logistical complexities, as adapting supply chains to green practices often requires significant adjustments and collaboration among partners.
Adapting to Market Changes
As market dynamics shift, inventory management must remain flexible. The capacity to adapt is crucial for businesses aiming to thrive. Understanding market trends and consumer behavior helps in successfully navigating the ever-evolving landscape.
Dynamic Inventory Strategies
Dynamic inventory strategies respond to real-time data and market conditions. These strategies provide businesses with the agility needed to meet changing customer demands. The key characteristic of dynamic strategies is their reliance on technology, including data analytics to forecast trends accurately.
A unique feature of dynamic strategies is their ability to minimize overstock and stockouts. By assessing inventory levels in real-time, businesses maintain the right balance. However, reliance on technology may introduce challenges, such as needing to invest in data management systems or facing cybersecurity threats.
Responsive Supply Chain Concepts
Responsive supply chain concepts are integral for businesses dealing with rapid market shifts. They emphasize quick adjustments to inventory levels based on customer demand. A key characteristic of these concepts is their focus on collaboration across the supply chain.
The unique strength of responsive supply chains lies in their capability to manage fluctuations effectively. Companies can capitalize on trends quickly. However, high reliance on collaborations may result in vulnerability to disruptions, particularly if partners do not align on shared goals.
Consumer Behavior Insights
Understanding consumer behavior is critical for effective inventory management. Insights into consumer preferences and trends inform inventory levels and product offerings. The key characteristic of this approach is its data-driven foundation, where businesses analyze consumer data to predict buying patterns.
The unique aspect of consumer behavior insights is that they help businesses reduce guesswork in inventory management. This accuracy aids in optimizing stock levels. One downside is that consumer preferences can be unpredictable, which can impose risks if businesses cannot adapt swiftly to sudden changes.
Epilogue
The conclusion serves as an essential component of this article on inventory process flow. It encapsulates the integral aspects discussed throughout the text, reinforcing their significance to effective inventory management. A clear understanding of the insights gained can greatly benefit professionals in optimizing their inventory processes.
Summary of Key Insights
This section aims to consolidate the central themes of inventory process flow. Understanding elements such as stock procurement, inventory tracking, and management practices enables businesses to identify inefficiencies. Recognizing key performance indicators, such as inventory turnover ratios, is critical. These indicators guide decision-making processes, leading to improved operational efficiency. Another vital takeaway is the impact of technology in inventory management; adopting tools like RFID technology or cloud-based software can streamline operations.
- Effective inventory management relies on data-driven strategies.
- Key components include procurement, tracking, and analysis of performance metrics.
- Technology plays a crucial role in modernizing processes.
By synthesizing these insights, businesses can shape more informed strategies that mitigate common pitfalls and leverage opportunities in their inventory processes.
Final Thoughts on Effective Inventory Management
Organizations should also emphasize continuous improvement by regularly reviewing performance metrics and technology integration. Collaboration across departments and with suppliers can enhance communication and understanding of the inventory process.
"The future of inventory management lies in embracing change, innovation, and the evolving landscape of consumer needs."
As professionals delve into efficient inventory management, the knowledge gathered from this article can serve as a foundational guide. Implementing best practices discussed will help businesses attain their inventory goals and enhance overall efficiency.