Understanding WMS for Small Warehouses: A Comprehensive Guide
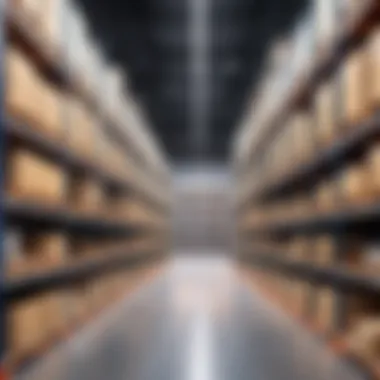
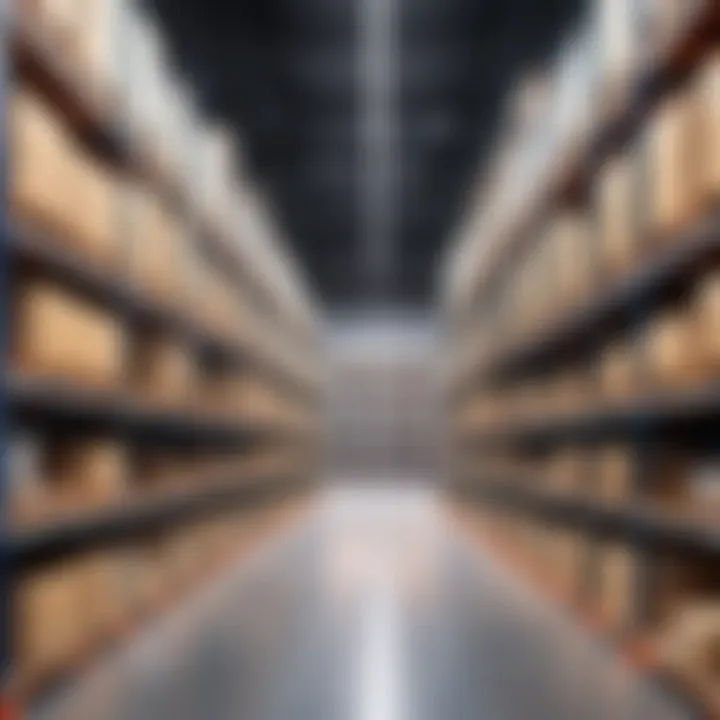
Intro
In today's fast-paced business environment, small warehouses play a crucial role in supply chain management. However, many of these small operations face unique challenges due to limited resources and space constraints. This is where Warehouse Management Systems (WMS) come into the picture. A well-implemented WMS can vastly improve operational efficiency, streamline processes, and enhance inventory control. This article will discuss the importance of WMS for small warehouses, the features of effective systems, and practical applications that can benefit these businesses.
Software Category Overview
Purpose and Importance
Warehouse Management Systems serve as the backbone of inventory management in small warehouses. Their primary purpose is to improve the accuracy of inventory tracking and to manage stock levels effectively. By automating processes, WMS reduces human error and increases efficiency. Moreover, these systems provide real-time data that is invaluable for decision-making. For small warehouses, where resources are already stretched, a WMS can optimize storage space and improve the picking and shipping processes.
Current Trends in the Software Category
In recent years, there has been a notable shift in WMS solutions. Many providers are focusing on cloud-based systems, which allow small warehouses to access advanced features without heavy upfront investment. Additionally, integration with technologies such as IoT and AI is becoming more common, allowing for smarter inventory management. As businesses demand more flexibility, mobile applications for WMS are increasingly popular. These trends indicate that even small warehouses can harness technology to remain competitive in a challenging market.
Data-Driven Analysis
Metrics and Criteria for Evaluation
Selecting the right WMS involves evaluating several key metrics:
- Cost vs. Value: Determine the total cost of ownership against the benefits expected.
- Scalability: Ensure that the system can grow with your business.
- Ease of Implementation: Assess how quickly and easily the system can be deployed.
- User Experience: Evaluate the interface and usability for staff.
- Integration: Check compatibility with existing systems and software.
Comparative Data on Leading Software Solutions
When considering different WMS options, it is critical to analyze the offerings of leading software solutions like SAP Extended Warehouse Management, Fishbowl Inventory, and Cin7. Each of these systems provides distinct advantages:
- SAP Extended Warehouse Management: Known for its robust capabilities, this solution is ideal for larger small warehouses that anticipate significant issues with scale.
- Fishbowl Inventory: This system is popular for small businesses seeking inventory management that's easy to set up and use.
- Cin7: Offers a comprehensive suite that integrates with e-commerce platforms.
These examples represent a range of functionalities suitable for various operational needs.
Prologue to WMS
Warehouse Management Systems (WMS) play a crucial role in the operational landscape of modern warehousing. Understanding WMS is vital for small warehouse owners who seek to improve their efficiency and manage their inventory better. This section will delve into the core aspects of WMS, exploring its definition and its significant role in the industry.
Defining Warehouse Management Systems
A Warehouse Management System is a software solution designed to optimize warehouse functionality and management. WMS solutions help you control various operations from inventory management to order fulfillment. By integrating a WMS into your warehouse, you can gain real-time visibility into inventory levels, optimize storage locations, and enhance overall workflow efficiency.
Some key functions of a WMS include:
- Inventory Control: Tracking inventory levels, locations, and movements.
- Order Management: Handling orders from receipt through to shipping.
- Reporting and Analytics: Providing insights into warehouse performance.
WMS can vary in complexity based on the warehouse size and operational needs. For small warehouses, a WMS designed with simplicity in mind can address unique challenges without overwhelming users with features that are unnecessary.
Importance of WMS in Warehousing
The significance of WMS in warehousing cannot be understated. The right WMS makes it possible for small warehouses to compete effectively in a dynamic market. Here are a few reasons why:
- Enhanced Operational Efficiency: A well-implemented WMS streamlines processes, reducing the time spent on tasks such as picking and packing.
- Improved Accuracy: Automated systems reduce human error. This means fewer misplaced items and more reliable service for customers.
- Better Inventory Management: With accurate tracking, businesses can prevent overstocking or stockouts. This balance leads to improved cash flow management.
"An effective WMS integrates all aspects of warehouse operations, providing a roadmap for growth and sustainability in the ever-evolving market."
Investing in a WMS is not just about software; it’s about redefining how your warehouse operates. As small warehouses adapt to the pressures of e-commerce and changing consumer demands, WMS technology emerges as a critical factor in long-term success.
The Unique Characteristics of Small Warehouses
Small warehouses play a distinctive role in today's supply chain ecosystem. This section explores their unique characteristics, which are essential for understanding how Warehouse Management Systems (WMS) can best cater to their needs. Recognizing these elements allows businesses to implement effective strategies that address both operational efficiencies and resource limitations.
Operational Challenges Faced by Small Warehouses
Small warehouses often deal with a range of operational challenges that set them apart from larger counterparts. Limited space is a prominent issue; efficient use of available area is critical while maintaining storage functionality. With less square footage, small warehouses must maximize inventory turnover, which requires precise tracking of stock levels and locations.
Moreover, staffing is another challenge. Small warehouses may have fewer employees, which increases the pressure on each staff member to multitask effectively. This can lead to higher susceptibility for human error, particularly in inventory management and order fulfillment. Adopting a WMS can be significant here by automating tasks, thus reducing reliance on manual processes.
Additionally, scaling operations can prove difficult due to the inflexible nature of smaller facilities. When demand increases, small warehouses must rapidly adjust. This requires dynamic solutions which often a robust WMS can provide, helping to streamline operations without requiring major physical changes.
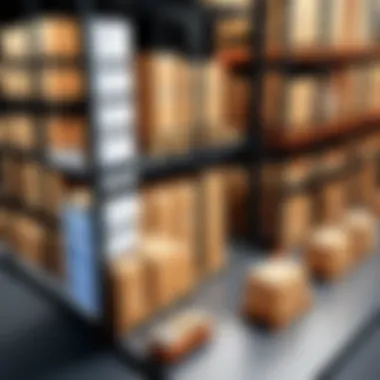
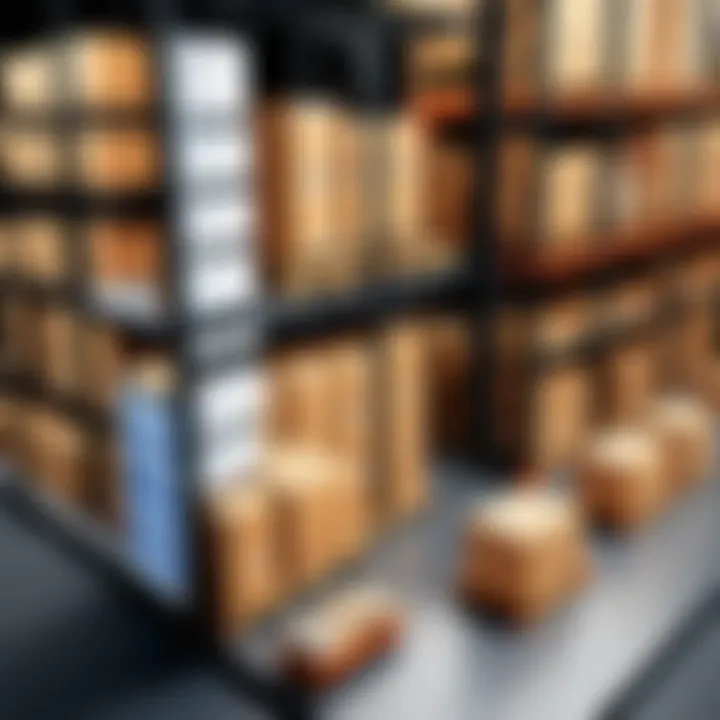
Resource Constraints and Their Implications
Resource constraints represent a crucial factor affecting small warehouses. Unlike larger operations that can spread costs over a broader base, small warehouses encounter tighter budgets. Limited financial resources restrict their ability to invest in advanced technologies and infrastructure, potentially putting them at a competitive disadvantage.
This limitation extends to staffing as well. Smaller teams often mean a lack of specialized roles, leading to potential inefficiencies. Understaffed warehouses can struggle to keep pace with demand, affecting customer satisfaction and delivery speeds. A WMS can help mitigate these resource constraints by improving process efficiencies and enabling better inventory management, thus optimizing labor usage.
"The efficient management of a small warehouse can often determine the agility of the entire supply chain."
By leveraging WMS, small warehouses can transform these challenges into opportunities for growth and increased service levels, paving the way for future success.
Key Features of WMS for Small Warehouses
Warehouse Management Systems (WMS) offer a variety of features that can transform the operations of small warehouses. In a sector where efficiency, accuracy, and cost-effectiveness are paramount, the right WMS can help optimize processes and ensure better inventory handling. This section will explore key features that small warehouses should consider when implementing a WMS.
Inventory Tracking and Management
Inventory tracking is one of the most critical features of any WMS. For small warehouses, effective inventory management ensures that products are where they need to be, thus minimizing delays in order fulfillment.
- Real-Time Tracking: This allows businesses to monitor stock movements instantly. Accurate tracking of inventory levels helps prevent overstocking or understocking.
- Barcode Scanning: Utilizing barcode technology facilitates quick and precise entry and retrieval of goods from inventory. This process reduces human errors significantly.
- Automated Reordering: When inventory levels fall below a predefined threshold, automated reorder notifications can help maintain optimal stock levels. This prevents potential sales losses due to stockouts.
Implementing such inventory management features can directly enhance operational efficiency.
Order Fulfillment Solutions
Efficient order fulfillment is essential for customer satisfaction and retention. A WMS designed for small warehouses should streamline this process from order receipt to delivery.
- Pick and Pack Automation: This feature simplifies how orders are processed. Automated pick lists and optimized packing functions can lead to faster order dispatch.
- Multi-Channel Order Management: With the rise of e-commerce, small warehouses must handle orders from various platforms. A good WMS can integrate seamlessly with online marketplaces, allowing for centralized order management.
- Shipping Integrations: Direct links to shipping carriers not only streamline the fulfillment process but also provide up-to-date shipping rates and tracking information. This enhances transparency with customers.
Overall, advanced order fulfillment features can significantly improve turnaround times and customer experiences.
Reporting and Analytics Capabilities
Leveraging data analytics is vital for strategic decision-making. A robust WMS should provide comprehensive reporting and analytics features that allow warehouse managers to derive actionable insights.
- Performance Metrics: Having access to key performance indicators (KPIs) such as order accuracy, fulfillment rates, and inventory turnover can help identify areas for improvement.
- Sales and Inventory Trends: Understanding historical sales data along with inventory trends allows for better forecasting. This can help in adjusting purchasing strategies and inventory levels according to market demands.
- Custom Report Generation: Many WMS solutions offer customizable report options. This enables managers to analyze different data points as per specific business needs, increasing the relevance of insights gained.
As a result, effective reporting and analytics features empower small warehouses to make informed decisions, tailor their operations, and stay competitive in a changing market.
"Leveraging the right features is key for small warehouses aiming to thrive in an increasingly complex logistics landscape."
In summary, adopting advanced features like inventory tracking, order fulfillment solutions, and reporting analytics could enhance productivity and efficiency within small warehouse operations.
Benefits of Implementing WMS in Small Warehouses
Implementing a Warehouse Management System (WMS) can significantly transform operations in small warehouses. The benefits extend beyond efficiency; they also include accuracy, cost savings, and more. It is crucial for warehouse managers and business owners to recognize these advantages when contemplating the adoption of a WMS.
Increased Efficiency and Productivity
The core benefit of a WMS is its ability to streamline operations. With various tasks automated, small warehouses can optimize their workflows. For example, automated inventory tracking reduces the time employees spend managing stocks. This means that warehouse personnel can focus on more crucial aspects of the operation, such as customer service and order fulfillment.
Consider the following points regarding increased efficiency:
- Real-time tracking: Real-time inventory data enables quick decisions, improving order accuracy.
- Optimized warehouse layout: A WMS can suggest the best storage practices based on inventory movement, which enhances space utilization.
In sum, these efficiencies lead to higher productivity levels, enabling small warehouses to manage increased demand without necessarily adding resources.
Enhanced Accuracy and Error Reduction
Accuracy in small warehouses is vital. Errors in inventory management can lead to customer dissatisfaction and financial loss. A WMS minimizes human error through automation and systematic checks. Using barcodes or RFID technology ensures that the right items are picked and shipped.
Moreover, automated reporting allows for consistency in tracking and managing stock levels. This feature further reduces discrepancies between actual and recorded inventories. For best results, consider implementing:
- Cycle counts: Regular system checks keep data accurate and up-to-date.
- Alerts and notifications: WMS can notify staff of low stock levels, which assists in timely reordering and avoids delays.
This level of accuracy not only reduces errors but also fosters confidence among customers. They can trust that their orders will be correct and promptly delivered.
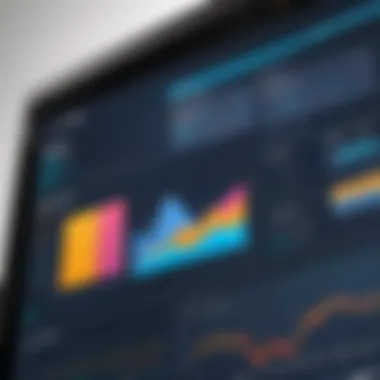
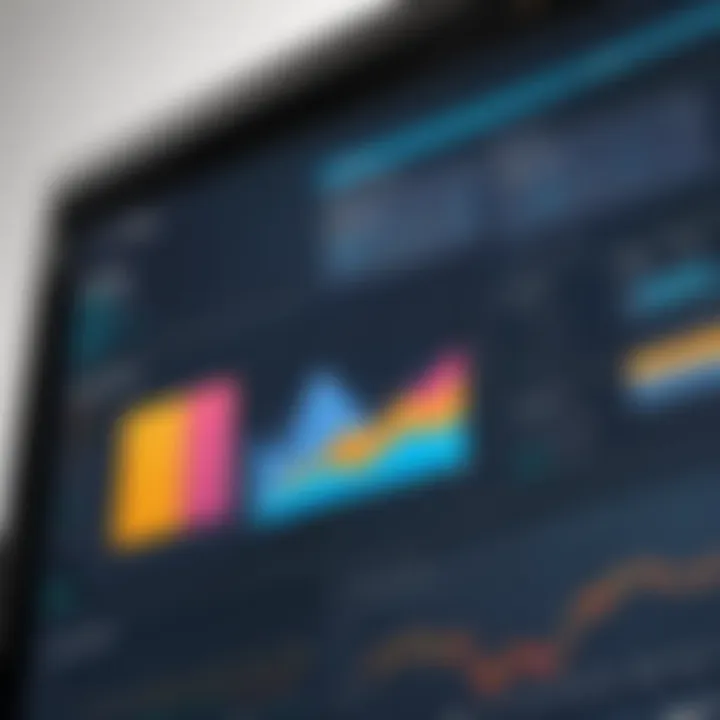
Cost Savings and ROI Considerations
Investing in a WMS may seem daunting for small warehouse operators, especially regarding cost. However, the long-term benefits usually outweigh the initial investment. Cost savings emerge through various channels, such as:
- Labor costs: Automation lowers the need for extensive manpower to manage warehouse tasks, resulting in reduced labor expenses.
- Error correction: With fewer inaccuracies, the costs tied to returns and corrections also decline.
- Improved space utilization: Efficient inventory management prevents excess stock and lowers storage costs.
When calculating the return on investment (ROI), consider not only the immediate savings but also the enhanced ability to meet future demands. A well-implemented WMS leads to increased capacity for managing orders without significantly increasing overheads.
Implementing a WMS is not just about technology; it is a strategic move towards operational excellence in small warehouses.
Challenges in Adopting WMS for Small Warehouses
Implementing a Warehouse Management System (WMS) in small warehouses can significantly transform operations. However, it involves navigating various challenges. Businesses must recognize these hurdles to make informed decisions about WMS solutions tailored to their unique contexts. Here, we explore the fundamental challenges that small warehouses face when adopting WMS.
High Initial Investment and Costs
The financial implications of adopting a WMS can be daunting for small warehouses. Initial investments typically include the cost of software, hardware, and training. Small businesses may find it challenging to allocate sufficient budget for these essential components. Indeed, costs can escalate rapidly without careful planning. Moreover, without a well-defined strategy, organization risks spending on features that might not deliver immediate value.
"Investing in WMS is not merely a purchase but a strategy that needs careful cost analysis."
To mitigate risks associated with high costs, small warehouses should conduct a thorough cost-benefit analysis before proceeding. This analysis should account for both initial expenses and potential long-term savings from improved efficiency. Identifying flexible pricing models or cloud-based solutions can also help in managing costs effectively.
Complexity of Implementation
Integrating a WMS into existing operations is often not straightforward. The complexity of implementing WMS can overwhelm small businesses that may have limited technical expertise. Many systems require a significant adjustment in workflows and processes, which can lead to operational disruption during the transition phase. Employees may also need extensive training to adapt to new systems.
Small warehouses should take a structured approach to this challenge. Defining clear implementation goals and timelines is essential. Involving key stakeholders early on, including staff from various departments, can also ease complexities. Organizations may benefit from phased rollouts, where the system is implemented in stages rather than all at once. This strategy helps in managing the learning curve while maintaining operations.
Resistance to Change within the Organization
Change is inherently challenging, especially in well-established small warehouses. Employees may resist adopting new technologies due to fear of disruption or job loss. This resistance can lead to decreased morale and operational efficiency. A significant challenge lies in overcoming this hesitance and fostering a culture that embraces innovation.
To combat resistance, organizations should communicate the benefits of WMS clearly. Offering incentives for early adopters and providing ongoing support can help in encouraging acceptance among staff. It is crucial to cultivate an environment where team members feel empowered to engage with the new system rather than fearing it. Furthermore, positive reinforcement through success stories from initial usage could encourage others to adapt over time.
Small warehouses must understand that while the transition to a WMS offers substantial benefits, recognizing and planning for these challenges is vital for successful implementation.
Evaluating WMS Options for Small Warehouses
Evaluating WMS options for small warehouses is a critical step in optimizing their operations. The effectiveness of a Warehouse Management System can significantly impact operations, inventory accuracy, and customer satisfaction. A thoughtful evaluation process ensures that small businesses find a solution suitable for their specific needs.
When evaluating WMS options, it is essential to keep several elements in mind:
- Business Requirements: A clear understanding of what functionalities are needed is essential. Different warehouses have varying needs, based on their operations, size, and type of inventory.
- Vendor Solutions: Assessing the solutions that vendors offer can help identify which system aligns best with the warehouse’s goals. This involves evaluating features, scalability, and user-friendliness.
- Cost-Benefit Analysis: It is crucial to analyze the financial implications of adopting a WMS. This includes initial costs and potential savings from improved efficiency.
Identifying the right WMS can lead to increased efficiency and better decision-making by providing reliable data insights.
Determining Business Requirements
Determining business requirements is the first step in evaluating a WMS. Understanding the specific needs of a small warehouse is vital for a good match between business processes and software functionalities. Key considerations include:
- Inventory Volume: The amount of inventory being managed will affect the types of features required. High volume may need advanced tracking systems.
- Order Types: Different order types, such as bulk or individual item orders, dictate different features in order fulfillment.
- Integration Requirements: Consideration of existing software systems is needed. A WMS should integrate seamlessly with current tools, such as accounting or e-commerce systems.
The goal is to create a list of must-have features that align with business goals and operational reality.
Assessing Vendor Solutions
Once business requirements are established, assessing vendor solutions becomes essential. This process includes:
- Feature Comparison: Review various WMS products to see which features meet the established requirements. A side-by-side comparison can be helpful.
- Demo and Trial Periods: Many vendors offer demo products or trial periods. Testing the software in real or simulated environments can provide insight into potential limitations.
- Customer Support and Training: Evaluate the level of customer support provided. Comprehensive training and support can ease the transition to a new system.
Involving key personnel in this evaluation ensures that the system chosen will fit the operational needs effectively.
Cost-Benefit Analysis
The final crucial step in evaluating WMS options is conducting a cost-benefit analysis. Understanding the financial impacts can help stakeholders make informed decisions. Important aspects include:
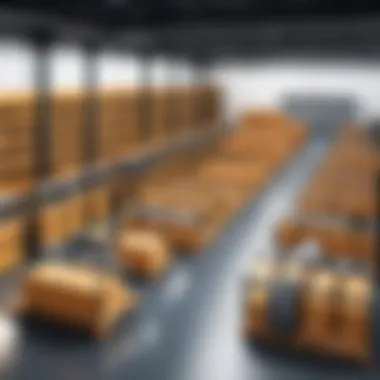
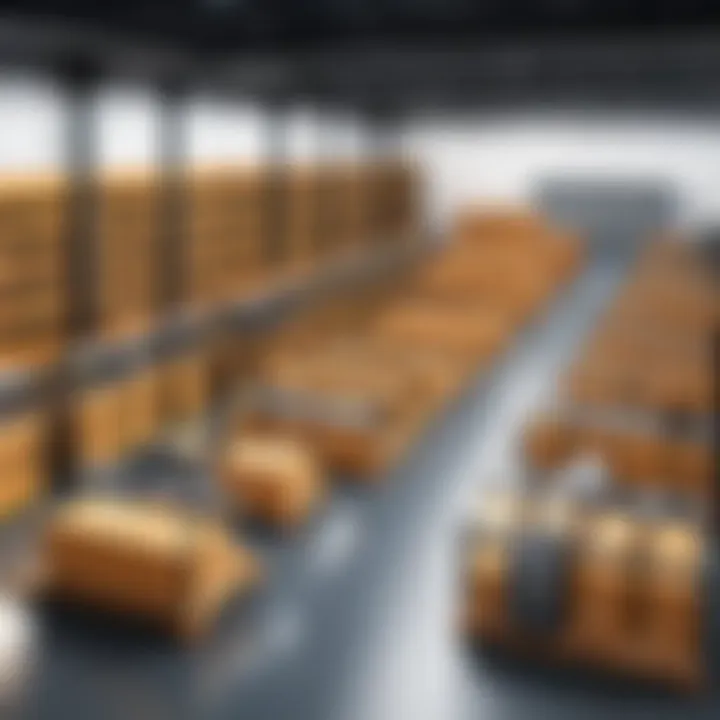
- Initial Costs: Examine the upfront costs of software, hardware, and installation. These costs should be weighed against the potential benefits.
- Ongoing Expenses: Consider maintenance fees and subscription costs. These recurring charges can accumulate significantly over time.
- Projected Savings: Assess potential savings from increased efficiency, reduced errors, and improved inventory management. Create scenarios illustrating how these savings can offset initial investments over time.
A well-rounded cost-benefit analysis will help determine if the investment in a new WMS is justified based on expected returns.
A systematic approach to evaluating WMS options can lead to substantial improvements in warehouse efficiency and profitability.
Integration of WMS with Existing Systems
Integrating a Warehouse Management System (WMS) within existing systems is crucial for small warehouses aiming to enhance their operational efficiency. This integration is not just about connecting software; it involves creating a seamless link between various operational components, such as inventory management, order processing, and accounting systems. A well-integrated WMS can significantly improve the workflow, reduce manual interventions, and enhance decision-making processes.
Compatibility with Other Software
Compatibility with other software is a primary consideration when selecting a WMS. Smaller warehouses often utilize various tools for accounting, customer relationship management (CRM), and logistics. Therefore, it is essential that the chosen WMS can interface smoothly with these existing applications.
- API Availability: Look for WMS solutions offering robust API functionality. This allows for easier integration with other systems.
- User Experience: A user-friendly interface can ease the transition and training process when integrating with existing systems.
- Data Format Compatibility: Ensure the WMS can handle the data formats used in other software solutions, facilitating accurate data exchange without loss.
Incompatibility can lead to data silos and significant inefficiencies. Ensuring compatibility enhances overall system performance.
Data Migration Strategies
Data migration is another integral aspect of integrating a new WMS. When transitioning to a new system, transferring existing data without errors is critical for ongoing operations.
- Data Cleansing: Before migration, it is necessary to clean the data to remove inaccuracies. This enhances data quality in the new system.
- Phased Migration: Consider a phased approach to migration. This allows for gradual adjustment to the new system instead of overwhelming employees.
- Backup Procedures: Regular backups should be made before and during the migration process to prevent data loss. This precaution ensures reliability and security.
Adopting these strategies can lead to a smoother transition and provide a solid foundation for the WMS's effective deployment.
"The ability to integrate WMS with existing software systems can make or break the efficiency of warehouse operations."
Future Trends in WMS for Small Warehouses
Warehouse Management Systems (WMS) play a crucial role in modern logistics, especially for small warehouses striving to stay competitive. The evolution of technology frequently influences how these systems operate, leading to significant advancements. Understanding future trends in WMS is essential to help small warehouse owners and managers anticipate changes and adapt accordingly.
Emerging technologies such as automation and artificial intelligence are becoming integral components of WMS. These tools not only improve operational efficiency but also enhance the accuracy of inventory management. In addition, the increasing demand from e-commerce presents its own challenges and opportunities for small warehouses. It is imperative to assess how WMS can alleviate pressure from growing customer expectations while still maintaining cost-effectiveness.
"The future of warehouses lies in their adaptability to technology trends that are shaping the e-commerce landscape."
The Influence of Automation and AI
Automation is no longer a luxury; it is becoming a necessity for small warehouses. By integrating automated systems, warehouses can streamline processes such as order picking, packing, and inventory tracking. This leads to faster order fulfillment and reduced labor costs. With advancements in robotics, small warehouses can now leverage automated guided vehicles (AGVs) and drones to enhance their operations.
Artificial Intelligence further augments these capabilities. AI algorithms can analyze historical data to predict future trends in demand, optimizing inventory levels. This results in a more responsive supply chain, minimizing the risks of stockouts or overstock. The combination of automation and AI serves not just to modernize operations but also to provide a competitive edge in a crowded market.
Adaptability to E-commerce Demands
The surge in e-commerce has altered customers' purchase behaviors, leading to higher expectations regarding shipment speed and accuracy. Small warehouses must adapt to these demands with agile WMS solutions. Robust systems now offer features capable of real-time inventory tracking and order processing, ensuring timely deliveries.
Moreover, flexibility in managing returns is becoming increasingly important. WMS equipped with advanced return management functionalities streamline the process, allowing warehouses to efficiently handle reverse logistics.
Culmination and Recommendations
The conclusion and recommendations segment serves as the capstone of the article, synthesizing the insights gained throughout the discussion on Warehouse Management Systems (WMS) for small warehouses. By revisiting critical points, this section reinforces the necessity of WMS adoption in today’s competitive market. As the landscape of warehousing continues to transform, small business operators must adapt in order to enhance their efficiencies and service capabilities.
Implementing a WMS tailored for small warehouses not only addresses immediate operational challenges but also sets a foundation for long-term growth. A well-integrated WMS can result in substantial improvements in inventory control, accuracy, and overall productivity. Therefore, decision-makers should not underestimate the intrinsic value a robust WMS brings to their operations.
Summarizing Key Points
In reflecting on the discussion points, several key areas deserve attention:
- Enhanced Efficiency: A WMS boosts operational workflows, streamlining tasks like order picking and inventory management, which can often be resource-intensive in small environments.
- Accuracy Improvements: Automation technologies reduce human error in stock management, resulting in more reliable inventory data.
- Cost-Effectiveness: Although the initial investment might be high, long-term financial benefits manifest through improved operational efficiencies and reduced labor costs.
- Analytics and Reporting: Advanced reporting features facilitate informed decision-making by providing real-time data insights.
These points outline just a few ways in which a WMS can revolutionize small warehouse functioning and performance.
Strategic Roadmap for Implementation
To successfully implement a WMS in a small warehouse, a strategic roadmap is essential. The following steps can guide organizations through this process:
- Conduct a Needs Assessment: Understand specific warehouse operational needs by examining inventory turnover rates, order volumes, and existing software solutions.
- Select the Right WMS: Research options that cater specifically to small warehouses. Popular choices may include Fishbowl, TradeGecko, or Cin7, among others. Consider features that align with the assessed needs.
- Plan for Data Migration: Develop a strategy for transferring existing data into the new WMS. This should include cleaning current data to ensure accuracy.
- Training Staff: Invest time in training employees on the new system. Their buy-in is critical to a successful transition.
- Monitor and Adjust: Once implementation is complete, closely monitor system performance and seek feedback from users to identify areas for adjustment.
Following this roadmap helps to ensure that the transition is not only smooth but also aligns with the strategic goals of the business. It is this methodical approach that fosters a successful adoption of WMS technology, delivering on promises of efficiency, accuracy, and enhanced service capabilities.
"A strategic roadmap enables organizations to systematically approach the complexity of WMS implementation with clarity and confidence."
By thoughtfully adopting these recommendations, small warehouse operators can significantly enhance their operations, positioning themselves for future success.